Sensors Series - Part 1 - Integrated Circuits
Sensors are the interface between the physical world determined by the laws of physics (i.e., mass, acceleration, conductivity, force, magnetic fields, etc.) and the digital world, which interprets the information that sensors provide for use in a wide range of products - from embedded Internet of Things (IoT) devices to smart phones to even the common household toaster. Because there are so many types of sensors available today, it would be a challenge to discuss all of them in one learning module. Since electronic design engineers often work with very compact integrated circuits (IC), this learning module will focus on some of the essential IC sensors in use today.
Related Components | Test Your Knowledge
sponsored by
2. Objectives
The objective of this learning module is to provide you with the essential knowledge of IC sensors. You will first review the purpose of IC sensors and what physical conditions or stimuli they sense. In subsequent sections of this learning module, you will gain an understanding of how sensors are classified as well as their characteristics and the types of commonly used IC sensors.
Upon completion of this learning module, you will be able to:
- Define a sensor
- Explain the difference between a sensor and a transducer
- Identify the types of physical conditions or stimuli that are measured by sensors
- Explain how sensors are classified
- Discuss the characteristics of sensors
- Identify the types and applications of capacitive, inductive, electrical current, smoke detection, and temperature sensors
- Describe the requirements of a MEMS sensor
3. Definition
What is a sensor? Or, what isn't a sensor? Let's begin this learning module with the definition of a sensor, which is sometimes confused with a similar term, transducer.
According to The Handbook of Modern Sensors: Physics, Designs and Applications, a sensor is defined as "a device that receives a stimulus and responds with an electrical signal."
Sensors are also called detectors, as well. But there is a slight difference between the terms and how they sense the physical world. Detectors sense information of a qualitative nature (i.e., presence of human movement), while a sensor measures physical stimuli quantitatively (i.e., ambient temperature in degrees Celsius). For the remainder of this learning module, we will use the terms "sensor" and "detector" as the same thing.
In some circles, the terms "sensor" and "transducer" are considered equivalent. But technically speaking, they are not. While it is true that a transducer receives a stimulus or a form of energy just like a sensor, a transducer's output is not an electrical signal; rather, the output of a transducer is another form of energy. In this context, a transducer is an energy converter.
A set of headphones is an example of a transducer since they convert an electrical signal into sound waves. A solar cell is also a transducer since it converts light energy into electrical energy. An electrical motor can be considered a transducer since it converts electrical energy (input voltage) into the mechanical energy (torque) needed to drive a rotating load (e.g., a centrifugal pump). But since it has a physical output, it is best characterized as an actuator.
What may cloud the meaning of the term sensor is a special category of sensor technology, the complex sensor. These sensors consist of various stages of sensing and transduction. For this learning module, we will define sensors and transducers as if they were simple sensors or transducers.

4. Classification
There are many types of sensors, ranging from displacement, level, velocity, acceleration, pressure, flow, humidity, ionizing radiation, temperature and many more. The growth of smart phones and the IoT has spawned the development of many more types of sensors, especially the highly integrated, intelligent, low-power sensors. As suggested in the previous sections, there are both simple and complex sensors. Yet these antipodal classifications do not represent all the different ways of classifying sensors. Knowing the classification of sensors can save an engineer a lot of time when he or she is trying to select a sensor for a circuit design. So, here are the main sensor classifications:
Passive and Active
Passive and active sensors are common ways of classifying sensors according to how their output signal is generated. Passive sensors do not require an external source of energy to produce an output signal. The energy of the input stimulus is converted by the sensor into an output electrical signal. A thermocouple is an example of a passive sensor. Conversely, active sensors do require an external source of energy (commonly called the excitation signal) to generate an output signal. The active sensor uses the excitation signal and modifies it to produce an output signal. An example of an active sensor is a temperature-sensitive resistor or thermistor. The excitation signal is modified by the resistor relative to temperature; variations based upon resistance can then be measured.
Absolute and Relative
Absolute and relative sensors are also two common ways of classifying sensors. However, these sensors are classified according to what reference is used to generate the output signal. Absolute sensors sense a stimulus that is referenced against an absolute scale and is independent of conditions. For example, a thermistor's output is referenced against the Kelvin temperature scale. Conversely, a relative sensor generates an output signal that is referenced against a special type of reference. For example, some pressure sensors are relative sensors because they use atmospheric pressure (14.696 psi) as the reference for their output signal.
Digital and Analog
Analog sensors are a type of sensor that produces an output signal that is continuous and proportional to the measurand. Digital sensors produce an output signal that is binary (0 or 1) and use analog to digital (A/D) data conversion.
Other Classifications
There are other ways to classify sensors, but, for the most part, these are for special situations. These special situations can include:
5. The Physical Stimuli of Sensing
Naturally, a sensor implies that "something" is sensed. So, let's now talk about what phenomena are sensed. Sensors are used to measure a variety of physical or material phenomena. These phenomena are sensed because they give us an objective "look" into the physical world, which is then converted into a form that embedded devices, computers and microcontrollers - the digital world - can understand and an engineer can employ in circuit designs.
The most common types of physical stimuli include acoustic, biological, chemical, electrical, magnetic, optical, thermal, radioactive, and mechanical. The following table summarizes the stimuli and the physical condition being sensed.
6. Sensor Characteristics
We had previously mentioned that sensor characteristics are a special way of classifying sensors. If you need to select a sensor for a circuit design, the usual place to begin the selection process is reading the sensor specs or characteristics listed in a datasheet. While datasheets are always informative, most of them do not explain all their terms.
So, in this section, we will define the characteristics of sensors, explaining them well enough so you can make an informed decision regarding the sensors you use. (Note: Since this is an Essentials learning module, the mathematical derivations of these characteristics will not be discussed.) Here are the definitions of the main characteristics of a sensor:
- Accuracy: the maximum difference that exists between the actual value and the indicated value at the output of the sensor. The accuracy can be expressed either as a percentage of full scale or in absolute terms.
- Dead band: the insensitivity of a sensor over a particular range of input signals, where the output stays at a certain value (typically zero) over the dead band.
- Drift: the gradual degradation of the sensor and other components that can make the sensor's output signal slowly change independently of the measurand.
- Hysteresis: a deviation error of the sensor's output at a specified point of the input signal when it is approached from the opposite direction (e.g. low-to-high versus high-to-low). The typical causes for hysteresis are the design, friction and structural changes in the materials.
- Linearity: When a sensor output is directly proportional to its input over the entire range.
- Nonlinearity: a maximum deviation error of the real transfer function when compared to the approximation of straight line.
- Offset: a type of error that represents the difference between the real output value and the specified output value under a particular set of conditions.
- Precision: the degree of reproducibility of a sensor's measured output.
- Range: the minimum and maximum values of a measurable input.
- Repeatability: a reproducibility error that is caused by the inability of a sensor to represent the same value under presumably identical conditions. The possible sources of a repeatability errors can be thermal noise, build up charge, material plasticity, etc.
- Resolution: the smallest change that can be detected by a sensor, expressed as a proportion of the reading (or the full-scale reading) or in absolute terms.
- Response Time: the time for a sensor to approach its true output when a stepped input change has occurred.
- Saturation: when a sensor's output signal is no longer responsive to a specific level of an input stimulus. Saturation exhibits a span-end, non-linearity.
- Sensitivity: the minimum input of physical parameter that will create a detectable change in output.
- Stability: the ability of a sensor to maintain its output parameter constant over time. Changes in stability, also known as drift, can be due to components aging, decrease in sensitivity of components, and/or a change in the signal to noise ratio.
7. Types of IC Sensors
IC sensors are the result of the new capabilities of large-scale, silicon processing that enables the inclusion of sensing and signal processing into a very compact, IC-sized package. As a result, electronics engineers now have a full palette of PCB-mountable sensors to employ in their circuit designs. IC sensors can sense a wide variety of physical conditions needed for the operation of consumer electronics devices, industrial control equipment, and embedded devices in IoT systems. The most commonly used IC sensors are grouped in the following categories:
- Capacitive
- Inductive
- Current
- Smoke Detection
- Temperature
- 7.1 Capacitive Sensors
Capacitive sensors are used detect and measure proximity, position or displacement, humidity, fluid level, acceleration and more. The ability of capacitive sensors to sense a wide range of materials makes capacitive sensing an ideal choice for many applications.
To understand how capacitance can be used as a sensing medium, let's review the definition of capacitance:
![]() |
C = Capacitance ε = Permittivity of the Dielectric A = Area of Plate Overlap d = distance between plates |
Capacitive sensors take advantage of the geometry of the flat capacitor, where capacitance as inversely proportional to the distance between the plates and directly proportional to the overlapping area of the plates. Thus, by changing the distance between the capacitor plates or the area of plate overlap, or causing variations in the dielectric material positioned between the plates, capacitance will be varied. This variable capacitance can then be used, along with a microcontroller and other signal conditioning circuitry, to produce an electrical output signal that's proportional to the change in capacitance as a result of the displacement.
The above scenario is realized in a popular application of capacitive sensing - touch sensing - used in tablets, smart phones and other types of touch pads. Capacitive touch sensing has become an alternative to traditional pushbutton switch, user interfaces because it requires no mechanical movement and it enables a completely sealed and modern-looking design.
A capacitive touch sensor is a copper sensor pad that's created on a printed circuit board that will have a parasitic capacitance to ground located elsewhere in the design. A covering plate is secured over the pad to create a touch surface.
Touching the covering plate over a pad creates an additional parallel capacitance essentially coupled to ground. This adds to the overall capacitance generated by the touch sensor used to detect a finger press.
The capacitance generated by the touch sensor is used in conjunction with a dual comparator with SR latch peripheral found on a Microchip PIC MCU along with external components to generate a relaxation oscillator. This configuration will generate an oscillation on the Q bar output of the SR latch. The frequency of oscillation will be determined by the capacitance, generated by the touch sensor and represented here by Cs. By itself, the capacitive touch sensor generates a particular frequency of oscillation.
The frequency of the oscillator is then measured in fixed intervals, using both Timer0 and Timer1 peripherals. Any shift due to a user's touch is detected and validated in software.
![]() Microchip CAP1208-1-A4-TR 8-Channel Capacitive Touch Sensor, QFNThe Microchip CAP1208 is a multiple channel capacitive touch sensor used in Desktop and Notebook PCs, LCD Monitors, Consumer Electronics and Appliances. It contains eight individual capacitive touch sensor inputs with programmable sensitivity for use in touch sensor applications. Each sensor input is calibrated to compensate for system parasitic capacitance and automatically recalibrated to compensate for gradual environmental changes. The CAP1208 includes Multiple Pattern Touch recognition that allows the user to select a specific set of buttons to be touched simultaneously. It also has Active and Standby states, each with its own sensor input configuration controls. Power consumption in the Standby state is dependent on the number of sensor inputs enabled as well as averaging, sampling time, and cycle time. Deep Sleep is the lowest power state available, drawing 5μA (typical) of current. In this state, no sensor inputs are active, and communications will wake the device. |
![]() Microchip CAP1298-1-A4-TR 8-Channel Capacitive Touch Sensor with Proximity Detection & Signal Guard, QFNThe Microchip CAP1298 is a multiple channel capacitive touch sensor used in computer, consumer electronics and appliances. While similar to CAP1208, the CAP1298 can also be configured to detect proximity on one or more channels with an optional signal guard to reduce noise sensitivity and to isolate the proximity antenna from nearby conductive surfaces that would otherwise attenuate the e-field. The CAP1298 also has Active and Standby states, each with its own sensor input configuration controls. The Combo state allows a combination of sensor input controls to be used which enables one or more sensor inputs to operate as buttons while another sensor input is operating as a proximity detector. |
![]() Microchip MTCH102-I/MS 8-Channel Proximity/Touch Controller MSOPThe Microchip MTCH102 provides an easy way to add proximity or touch detection to any application with human machine interface. It can integrate up to two, five and eight capacitive touch/proximity detection sensors which can work through plastic, wood or even metal front panels with Microchip's proprietary Metal over Capacitive technology. It also supports a wide range of conductive materials as sensors, like copper pad on PCB, silver ink, PEDOT or carbon printing on plastic film, Indium Tin Oxide (ITO) pad, wire/cable, etc. The MTCH102 uses a sophisticated scan optimization algorithm to actively attenuate noise from the signal. The sensitivity adjustment and flexible power mode allow users to easily configure the device at run-time. An active-low output will communicate the state of the sensors to a host/master MCU or drive an indication LED. |
![]() Microchip MTCH101-I/OT Single-Channel Proximity Detector SOT-23The Microchip MTCH101 provides an easy way to add proximity or touch detection to any human interface application. The device integrates a single-channel capacitive proximity detection, which can work through plastic, glass or wood-front panel. It also supports a wide range of conductive materials as sensor, like copper pad on PCB, silver or carbon printing on plastic, Indium Tin Oxide (ITO) pad, wire/cable, etc. On-board adjustable sensitivity and power mode selection allow the user to configure the device at run time easily. An active-low output will communicate the state of the sensor to a host/master MCU, or drive an indication LED. |
- 7.2 Inductive Sensors
Inductive sensors are a type of displacement sensor used to sense changes in position, distance and proximity. One of the advantages of inductive sensing is that non-magnetic materials (e.g., stainless steel, brass, plastics, woods, and others) can be penetrated by a magnetic field without any loss of positional accuracy. Another differentiating advantage of inductive sensors is that they can work in severe environments where capacitive sensors cannot.
Inductive touch sensors are a common replacement for electromechanical pushbutton switches in severe or outdoor environments. An inductive touch system uses the magnetic coupling between a solid metal target and an inductive sensing coil. The target is a passive, electrically conductive layer that is arranged to displace or deform along the measurement axis relative to the coil. The sensor coils are one or more inductors, implemented as flat spiral coils, etched into the copper layer of a PCB. The inductance of the coil is determined by the number of turns and the dimensions of the pattern etched into the PCB.
If a user presses on the front panel, then the coupling between the target and sense coil will change due to the minute shift in the target's position. When the user presses the front panel, it deflects slightly. This deflection, on the order of microns, is inductively detected.
![]() Side View - Inductive Touch Sensor |
![]() Top View - Spiral Coil |
The fundamental principle of operation of inductive touch technology is that the inductance of an inductor varies when a nearby magnetically permeable or electrically conductive material moves relative to the inductor. This is because the magnetically permeable or electrically conductive material provides an alternative route for the magnetic flux which, in turn, varies the inductance. The closer the material is to the inductor, the greater the effect. The coil's inductance decreases as the target approaches and, to a limit, vice versa.
![]() Microchip MCP2036-I/SL Inductive Sensor Analog Front End Device SOICThe Microchip MCP2036 Inductive Sensor Analog Front End (AFE) combines all the necessary analog functions for a complete inductance measurement system. The MCP2036 measures a sensor coil's impedance by exciting the coil with a pulsed DC current and measuring the amplitude of the resulting AC voltage waveform. The drive current is generated by the on-chip current amplifier/driver which takes the high-frequency triangular waveform present on the DRVIN input, and amplifies it into the pulsed DC current for exciting the series combination of the sensor coils. The AC voltages generated across the coils, are then capacitively coupled into the LBTN and LREF inputs. An input resistance of 2K between the inputs and the virtual ground offsets the AC input voltages up to the signal ground generated by the reference voltage generator. |
- 7.3 Current Sensors
Current sensors detect electrical circuit path current and convert it to an output voltage, which is proportional to the current through the measured path. There are a wide variety of current sensors, with each type rated for a specific current range and environmental condition. Many power and control applications benefit from current sensing, including battery life indicators and chargers, current and voltage regulators, DC/DC converters, ground fault detectors, linear and switch-mode power supplies, automotive power electronics and motor speed controls.
Current Sensing Resistors
Current sensing resistors are the most commonly used way to sense current. They can be considered a current-to-voltage converter, where inserting a resistor into the current path, the current is converted to voltage in a linear way of V = I x R. The main advantages and disadvantages of current sensing resistors include:
Advantages | Disadvantages |
|
|
The disadvantages can be somewhat overcome by using low-value sensing resistors. However, the voltage drop across the sensing resistor may become low enough to be comparable to the input offset voltage of subsequent analog conditioning circuit, which would compromise the measurement accuracy.
In addition, if the measured current has a large high-frequency component, the current sensing resistor's inherent inductance must be low. Otherwise, the inductance can induce an Electromotive Force (EMF) which will degrade the measurement accuracy as well. Furthermore, the resistance tolerance, temperature coefficient, thermal EMF, temperature rating and power rating are also important parameters of current sensing resistors when measurement accuracy is required.
Current Sensing Techniques
Low-side and high-side current sensing are two common techniques for sensing for circuit current. Low-side current sensing connects the sensing resistor between the load and ground, while high-side current sensing connects the sensing resistor between the power supply and load.
A) Low-side sensing is advantageous because common-mode voltage is near ground potential, providing for the use of single-supply, rail-to-rail input/output op amps. Normally, the sensed voltage signal (VSEN = ISEN x RSEN) is so small that it needs to be amplified by subsequent op amp circuits (e.g., non-inverting amplifier) to get the measurable output voltage (VOUT).
Advantages | Disadvantages |
|
|
B) High-side current sensing connects the sensing resistor between the power supply and load. The sensed voltage signal is amplified by subsequent op amp circuits to get the measurable VOUT. High-side current sensing is typically selected in applications where ground disturbance cannot be tolerated, and short circuit detection is required, such as motor monitoring and control, overcurrent protection and supervising circuits, automotive safety systems, and battery current monitoring.
Advantages | Disadvantages |
|
|
![]() Microchip EMC1701-2-AIZL-TR High-Side Current-Sense and Internal 1°C Temperature Monitor MSOPThe Microchip EMC1701 is a combination high-side current sensing device with precision temperature measurement for Notebook and Desktop Computers, Industrial Equipment, Power Management Systems and Embedded Applications. It measures the voltage developed across an external sense resistor to represent the high-side current of a battery or voltage regulator. The EMC1701 also measures the source voltage and uses these measured values to present a proportional power calculation. The EMC1701 contains additional bi-directional peak detection circuitry to flag instantaneous current spikes with programmable time duration and magnitude threshold. Finally, the EMC1701 includes an internal diode channel for ambient temperature measurement. Both current sensing and temperature monitoring include two tiers of protection: one that can be masked and causes the ALERT pin to be asserted, and the other that cannot be masked and causes the THERM pin to be asserted. |
![]() Microchip PAC1710-1-AIA-TR Single High-Side Current Sense Monitor with Power Calculation DFNThe Microchip PAC1710 is a high-side bi-directional current sensing monitor with precision voltage measurement capabilities. The power monitor measures the voltage developed across an external sense resistor to represent the high-side current of a battery or voltage regulator. The PAC1710 also measures the SENSE+ pin voltage and calculates average power over the integration period. The PAC1710 can be programmed to assert the ALERT pin when high and low limits are exceeded for Current Sense and Bus Voltage. Available in a RoHS compliant 3 X 3mm 10-pin DFN package. |
- 7.4 Smoke Detection Sensors
Smoke detection sensors are used in both residential and commercial alarms throughout the world. They come in two forms: photoelectric and ionization. Photoelectric smoke detectors use a light source to detect smoke, while ionization smoke detectors use a radioisotope to ionize air. Performance-wise, photoelectric smoke detectors respond faster to a fire in its early stage because the detectors are more sensitive to the large combustion particles that emanate during slow, smoldering fires. Conversely, ionization smoke alarms respond faster to fast flaming fires because they can detect small amounts of smoke produced by fast flaming fires, such as cooking fires or fires fueled by paper or flammable liquids.
![]() Microchip RE46C141S16F CMOS Photoelectric Smoke Detector ASIC with Interconnect SOICThe Microchip RE46C141 is low power CMOS photoelectric type smoke detector IC. With minimal external components this circuit will provide all the required features for a photoelectric type smoke detector. The design incorporates a gain selectable photo amplifier for use with an infrared emitter/detector pair. An internal oscillator strobes power to the smoke detection circuitry for 100µs every 8.1 seconds to keep standby current to a minimum. If smoke is sensed the detection rate is increased to verify an alarm condition. A high gain mode is available for push button chamber testing. A check for a low battery condition and chamber integrity is performed every 32 seconds when in standby. The temporal horn pattern supports the NFPA 72 emergency evacuation signal. An interconnect pin allows multiple detectors to be connected such that when one units alarms, all units will sound. The RE46C141 is recognized by Underwriters Laboratories for use in smoke detectors that comply with specification UL217 and UL268. |
![]() Microchip RE46C166S16F CMOS Photoelectric Smoke Detector ASIC with Interconnect Timer Mode and Alarm Memory SOICThe Microchip RE46C166 device is low-power, CMOS photoelectric type, smoke detector ICs. Each design incorporates a gain selectable photo amplifier for use with an infrared emitter/detector pair. An internal oscillator strobes power to the smoke detection circuitry for 100 μs every 10 seconds to keep standby current to a minimum. If smoke is sensed, the detection rate is increased to verify an alarm condition. A high gain mode is available for push button chamber testing. A check for a low battery condition and chamber integrity is performed every 43 seconds when in standby. The temporal horn pattern supports the NFPA 72 emergency evacuation signal. An interconnect pin allows multiple detectors to be connected so when one unit alarms, all units will sound. A charge dump feature will quickly discharge the interconnect line when exiting a local alarm. The interconnect input is also digitally filtered. An internal timer allows for single button, push-to-test to be used for a reduced sensitivity mode. An alarm memory feature allows the user to determine if the unit has previously entered a local alarm condition. The RE46C166 was designed for use in smoke detectors that comply with Underwriters Laboratory Specification UL217 and UL268. |
![]() Microchip RE46C180E16F CMOS Programmable Ionization Smoke Detector ASIC with Interconnect Timer Mode and Alarm Memory DIPThe Microchip RE46C180 is a low power, CMOS ionization-type, smoke detector IC. With minimal external components, this circuit will provide all the required features for an ionization-type smoke detector. An on-chip oscillator strobes power to the smoke detection circuitry for 5 ms every 10 seconds to keep the standby current to a minimum. A check for a Low Battery condition is performed every 80s and an ionization chamber test is performed once every 320s when in Standby. The temporal horn pattern complies with the National Fire Protection Association NFPA 72 An interconnect pin allows multiple detectors to be connected, such that when one unit alarms, all units will sound. A charge dump feature quickly discharges the interconnect line when exiting a Local Alarm condition. The interconnect input is also digitally filtered. An internal 9 minute or 80s timer can be used for a Reduced Sensitivity mode. An alarm memory feature allows the user to determine whether the unit has previously entered a Local Alarm condition. The RE46C180 is designed for use in smoke detectors that comply with the Standard for Single and Multiple Station Smoke Alarms, UL217 and the Standard for Smoke Detectors for Fire Alarm Systems, UL268. |
![]() Microchip RE46C190S16F CMOS Low Voltage Photoelect ric Smoke Detector ASIC with Interconnect and Timer Mode SOICThe Microchip RE46C190 is a low power, low voltage CMOS photoelectric type smoke detector IC. The design incorporates a gain-selectable photo amplifier for use with an infrared emitter/detector pair. An internal oscillator strobes power to the smoke detection circuitry every 10 seconds, to keep the standby current to a minimum. If smoke is sensed, the detection rate is increased to verify an Alarm condition. A high gain mode is available for push button chamber testing. A check for a low battery condition is performed every 86 seconds, and chamber integrity is tested once every 43 seconds, when in Standby. The temporal horn pattern supports the NFPA 72 emergency evacuation signal. An interconnect pin allows multiple detectors to be connected such that, when one unit alarms, all units will sound. An internal 9 minute timer can be used for a Reduced Sensitivity mode. The RE46C190 was designed for use in smoke detectors that comply with Underwriters Laboratory Specification UL217 and UL268. |
- 7.5 Temperature Sensors
Temperature sensing is a fundamental function of control systems in many types of appliances, handheld devices, industrial equipment, as well as others. There are a number of passive and active temperature sensors that can be used to measure system temperature, including thermocouples, resistive temperature detectors (RTDs), thermistors and silicon temperature sensors. These sensors provide temperature feedback to a system controller that oversees control functions such as over-temperature shutdown, turn-on/off cooling fan, temperature compensation, or as a general purpose temperature monitor.
![]() Microchip MCP9701AT-E/TT Low-Power Linear Active Thermistor
|
![]() Microchip TC77-3.3MCTTR Digital Thermal Sensor with SPI
|
![]() Microchip TC622CPA Low Cost Single Trip Point Temperature Sensor DIPThe TC622 is a single point, programmable solid-state temperature sensors designed to replace mechanical switches in sensing and control applications. Both devices integrate the temperature sensor with a voltage reference and all required detector circuitry. The desired temperature set point is set by the user with a single external resistor. Ambient temperature is sensed and compared to the programmed set point. The OUT and OUT outputs are driven to their active state when the measured temperature exceeds the programmed set point. The TC622 has a power supply voltage range of 4.5V to 18.0V while the TC624 operates over a power supply range of 2.7V to 4.5V. It has a usable temperature range of -40°C to +125°C (TC622VXX). The device features low supply current making it suitable for portable applications. Eight-pin through-hole and surface mount packages are available. The TC622 is also offered in a 5-pin TO-220 package. |
![]() Microchip TC74A0-5.0VAT Tiny Serial Digital Thermal Sensor TO-220The Microchip TC74 is a serially accessible, digital temperature sensor particularly suited for low cost and small form-factor applications. Temperature data is converted from the onboard thermal sensing element and made available as an 8-bit digital word. Communication with the TC74 is accomplished via a 2-wire SMBus/I2C compatible serial port. This bus also can be used to implement multi-drop/multi-zone monitoring. The SHDN bit in the CONFIG register can be used to activate the low power Standby mode. Temperature resolution is 1°C. Conversion rate is a nominal 8 samples/sec. During normal operation, the quiescent current is 200 μA (typ). During standby operation, the quiescent current is 5 μA (typ). Small size, low installed cost and ease of use make the TC74 an ideal choice for implementing thermal management in a variety of systems. |
![]() Microchip MCP98244T-BE/MNY DDR4 DIMM Temperature Sensor with EEPROM for SPD, TDFNThe Microchip MCP98244 digital temperature sensor converts temperature from -40°C and +125°C to a digital word. This sensor meets JEDEC Specification JC42.4-TSE3000B1 Memory Module Thermal Sensor Component. It provides an accuracy of ±0.2°C/±1°C (typical/maximum) from +75°C to +95°C with an operating voltage of 1.7V to 3.6V. In addition, MCP98244 has an integrated EEPROM with two banks of 256 by 8 bit EEPROM (4k Bit) which can be used to store memory module details and vendor information. The MCP98244 digital temperature sensor comes with user-programmable registers that provide flexibility for DIMM temperature-sensing applications. The registers allow user-selectable settings such as Shutdown or Low-Power modes and the specification of temperature Event boundaries. When the temperature changes beyond the specified Event boundary limits, the MCP98244 outputs an Alert signal at the Event pin. The user has the option of setting the temperature Event output signal polarity as either an active-low or active-high comparator output for thermostat operation, or as a temperature Event interrupt output for microprocessor-based systems. The MCP98244 EEPROM is designed specifically for DRAM DIMMs (Dual In-line Memory Modules) Serial Presence Detect (SPD). It has four 128 Byte pages, which can be Software Write Protected individually. This allows DRAM vendor and product information to be stored and write-protected. This sensor has an industry standard I2C Fast Mode Plus compatible 1 MHz serial interface. |
![]() Microchip MCP9904T-2E/9Q Multi-Channel Low-Temperature Remote Diode Sensor VDFNThe Microchip MCP9904 is a high-accuracy, low-cost, System Management Bus (SMBus) temperature sensor. The MCP9904 monitors up to four temperature channels. Advanced features such as Resistance Error Correction (REC), Beta Compensation (to support CPU diodes requiring the BJT/transistor model including 45 nm, 65 nm and 90 nm processors) and automatic diode-type detection combine to provide a robust solution for complex environmental monitoring applications. Resistance Error Correction automatically eliminates the temperature error caused by series resistance allowing greater flexibility in routing thermal diodes. Beta Compensation eliminates temperature errors caused by low, variable beta transistors common in today's fine geometry processors. The automatic beta detection feature monitors the external diode/transistor and determines the optimum sensor settings for accurate temperature measurements regardless of processor technology. This frees the user from providing unique sensor configurations for each temperature monitoring application. These advanced features plus ±1°C measurement accuracy for both external and internal diode temperatures provide a low-cost, highly flexible and accurate solution for critical temperature monitoring applications. |
- 7.6 Micro-Electro-Mechanical Systems (MEMS) Sensors
The ability to microengineer and micromachine components with dimensions on the order of micrometers has brought forth the development of MEMS technology. MEMS is a micro-electro-mechanical system consisting of microcomponents of mechanical and electrical devices that enable the manufacturing of microsensors and actuators in combination with control and signal conditioning circuitry. MEMS are appearing in monitoring and control of applications ranging from biomedicine to IoT embedded systems to smart phones to automated manufacturing.
![]() Microchip MM7150-AB0 MEMS Module Tri-Axis Gyroscope Tri-Axis Accelerometer Tri-Axis Magnetometer 2g ModuleThe Microchip MM7150 Motion Module is a simple, cost-effective solution for integrating motion and positioning data into a wide range of applications. The module contains the SSC7150 motion coprocessor with integrated 9-axis sensor fusion as well as high performance MEMS technology including a 3-axis accelerometer, gyroscope and magnetometer. All components are integrated, calibrated and available on the module for PCB mounting. |
*Trademark. Microchip
is a trademark of Microchip Technology Inc. Other logos, product and/or company names may be trademarks of their respective owners.
Test Your Knowledge
Sensor Skills 1
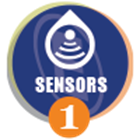
Are you ready to demonstrate your IC Sensors knowledge? Then take a quick 20-question multiple choice quiz to see how much you've learned from this Essentials Sensors 1 module.
To earn the Sensors 1 badge, read through the module to learn all about IC Sensors, attain 100% in the quiz at the bottom, leave us some feedback in the comments section and bookmark this page.
Top Comments