An overview of new innovations in the design of modern EV chargers.
The different types of EV chargers
To hasten the adoption of electric vehicles (EVs), charging infrastructure must become more accessible, convenient, and reliable. The development of fast-charging stations is also critical, because consumers want charging to be quick and easy, much like refueling an ICE vehicle. Currently, there are three common charging methods - Level 1, 2, and DC Fast Charging. While industry experts consider Level 1 and Level 2 chargers as standard "wall sockets", DC Fast Chargers are a real game-changer. With DC Fast Charging, the onboard charger is bypassed and the battery is charged directly, drastically reducing charging time. For example, many DC Fast Chargers can provide 80% charge in as little as 15 minutes. This article discusses innovative EV charging solutions, focusing on fast charger design requirements and the growing network of fast charging stations.
What is a Fast Charger?
Onboard chargers (OBCs) enable a vehicle to be charged using a standard plug (slow AC) or a specialized AC charger (moderate AC) at a home, workplace, or public location. The AC power that comes from domestic sockets is converted to DC for storage in batteries. In an EV, this conversion is performed by the OBC. The OBC AC charger is typically a 7 kW unit that charges a vehicle via a single-phase domestic main’s supply. Some homeowners may also opt for a three-phase charger, delivering up to 22 kW to the vehicle.
Figure 1: AC and DC Charging in an Electric Vehicle (Source: TE Connectivity)
DC Fast Charging bypasses all the limitations inherent within the OBC and provides DC power directly to the battery, greatly increasing the charging speed. DC Fast Chargers are referred to as Level 3 Chargers. Charging can be either rapid or ultra-rapid, depending on the power delivered. The power range starts at around 50 kW (rapid) and can reach 350 kW (ultra-rapid). Table 1 details the different charger power level types.
Power Level Types | Charger Location | Typical Use | Energy Supply Interface | Expected Power Level | Charging Time |
---|---|---|---|---|---|
Level 1 (Slow) | On-board 1-phase (AC charging) | Charging at home or office | Convenience outlet | 1.4kW (12A) 1.9kW (20A) |
11-36 hours 4-11 hours |
Level 2 (Intermediate or slow) | On-board 1- or 3-phase (AC charging) | Charging at private or public outlets | Dedicated power connector | 4kW (17A) 8kW (32A) 19.2kW (80A) |
2-6 hours 2-3 hours 1-4 hours |
Level 3 (Fast/less than 1 hour) | Off-board 3-phase (DC charging) | Commercial, same as gas station | Dedicated power connector | 50kW 100kW 250kW 350kW |
0.4-1 hours 0.2-0.5 hours |
Table 1: The levels of EV chargers (Source: Avnet)
Fast chargers are designed to protect users and their vehicles against excess currents, leakage currents, and high-temperatures. The vehicle's battery management system (BMS) provides additional measures to detect and help avoid potential problems.
Figure 2: Three-phase EV DC Charger (Source: Avnet)
Figure 2 illustrates the general outline of an EV DC charger. An EV DC charger typically uses a three-phase AC supply. The implementation of various power stages depends on the power level, with different conversion topologies having trade-offs in efficiency, potential EMI, complexity, cost, functionality, and bi-directional ability.
An EV DC charger typically takes the AC feed from the mains (between 100 and 400V) and passes the current through a full-wave rectifier and smoothing filter. The DC-DC conversion block consists of a low-power DC-DC converter that drives silicon carbide (SiC) or IGBT high-power switching devices. Engineers must balance between maximizing system efficiency through fast switching and minimizing EMI or noise though use of lower switching frequencies. DC charging systems require heavy-duty electrical engineering, interconnect, and cabling components. Technology advancements like wide-bandgap semiconductors and innovative converter topologies improve conversion efficiencies, reducing waste heat dissipation, easing thermal management challenges, and improving component reliability characteristics.
What are the challenges of designing a Fast Charger?
DC fast chargers can deliver higher power levels to EVs; however, this can stress local power distribution infrastructure, causing voltage fluctuations, dips, and waveform distortion and resulting in overall grid instability. DC Fast Chargers can also overload the distribution transformer and inject unwanted harmonic content.
Connectors & Power Electronics
Shop our wide variety of Connectors and Power Electronics from TE Connectivity.
Don't forget to join our discussion.
Other design techniques
Fast chargers are designed to provide a quick and seamless experience for electric vehicle users. They utilize innovative engineering solutions, advanced cooling techniques, and multi-standard support, with a focus on safety and reliability. Fast chargers use techniques such as multistage constant current (MCC) charging, pulse charging, boost charging, and variable current profiles (VCPs) to reduce charging time without reducing the useful lifetime of the battery. DC Fast Chargers may require increased transformer capacity, upgraded substations, and reinforced distribution lines to accommodate increased power demand. Power factor correction (PFC) stages reduce harmonics injected into the power grid, while optocouplers improve power factor and generate regulated DC output voltage for the downstream DC-DC converter. Additionally, advanced cooling techniques, such as liquid cooling and heat pipes, are used to maintain optimal operating temperatures and ensure the reliability of fast-charging electronics.
Miniaturization of EV Chargers
Advancements in power conversion topologies are paving the way for bidirectional, high-power density, and scalable converters. Materials like silicon carbide (SiC) and gallium nitride (GaN) offer higher efficiency and superior thermal properties when compared to traditional silicon-based components. This has led to the development of portable chargers with fast charging capabilities. These portable chargers are compact, handheld devices with natural convection cooling, capable of switching at a wide range of frequencies. High-power portable chargers, also known as fleet chargers, require sophisticated multilevel three-phase power factor correction (PFC) and DC-DC stages to deliver substantial power.
Components for EV Chargers
TE Connectivity offers a broad portfolio of relays, physical connectors, passives, switch components, and electrical products for EV charging applications with a wide range of power levels.
Summing Up: Designing EV Chargers
In partnership with
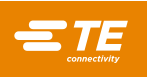
Consumers will purchase EVs in much higher numbers when they are confident that the charging infrastructure is reliable and widespread, and won’t leave them stranded. DC Fast Charging improves the driving experience by reducing charging times and accelerating charging speeds; however, challenges such as voltage fluctuation and power quality must be considered during the design stage. TE Connectivity manufactures a variety of components that are well-suited for use in DC Fast Chargers, and small form factor portable EV chargers
Click here for more information about EV Charging.
How long do you think it will be before EVs are powered completely by renewable energy?
Please tell us in the Comments section below.