This Tech Spotlight discusses the modern battery management system (BMS), its functionality, and the components and architecture inside. A BMS monitors and controls the health, state of charge, and temperature of individual battery cells to optimize performance, ensure safety, and prolong the battery's lifespan. This is essential for lithium-ion (Li-ion) batteries, which are susceptible to risks including overheating, mechanical stress, over-current, and deep discharge.
What does a BMS do?
A BMS (Figure 1) constantly monitors varying battery states and characteristics to maintain operational conditions and minimize safety risks. A BMS can detect battery type, monitor voltages, state of charge, charging cycles, temperature, capacity, power consumption, and remaining operating time, among other characteristics. The BMS also ensures that a battery pack is charged and/or discharged safely. These functions minimize poor performance and prevent failures in EV energy storage systems. A BMS must also be compact and lightweight, adding minimal bulk to the overall battery pack geometry.
Figure 1: Basic structure of a BMS (Source: TE Connectivity)
Figure 2: Charging – Discharging curves of Lithium-ion batteries (Source: Battery University)
Figure 2 depicts the voltage and current curves as Li-ion passes through the constant current and topping charge stages. Proper handling is important for battery longevity, safety, and optimal performance. Temperature also plays a significant role. High temperatures can accelerate chemical reactions, causing faster degradation and reduced capacity, while cold temperatures slow reactions, potentially limiting power delivery.
Excessive charging or draining of the battery can also damage its internal chemistry, leading to capacity loss, reduced performance, and safety risks. Manufacturers recommend using chargers designed explicitly for their batteries to minimize (or eliminate) this issue. Deep discharges can increase wear and tear on Li-ion batteries, while shallower discharges prolong battery life. A BMS prevents charging beyond safe voltage limits and discharging below minimum levels, protecting against capacity degradation and other safety hazards. It monitors battery temperature and adjusts charging rates to avoid overheating. In multi-cell battery packs, a BMS ensures that each cell is equally charged and discharged, preventing imbalances that could lead to overcharging or over-discharging. Lastly, a BMS accurately estimates the battery's remaining charge, helping users plan operations and prevent unexpected shutdowns caused by depleted batteries.
How long does an Li-ion battery last?The lifespan of a Li-ion (Lithium-ion) battery can vary significantly depending on several factors, including usage patterns, temperature conditions, and the quality of the battery. Generally, a Li-ion battery is considered to have a lifespan of around 300 to 500 charge-discharge cycles, where a cycle typically involves using around 80% of the battery's capacity. However, many modern Li-ion batteries can last longer when well-maintained and used under optimal conditions. With proper care, they can retain a significant portion of their capacity for several years. It's important to note that over time, even well-maintained Li-ion batteries will naturally degrade and eventually lose their ability to hold a charge effectively. Factors like high temperatures, frequent deep discharges, and overcharging can accelerate battery degradation, while keeping the battery at moderate temperatures and avoiding extreme charge and discharge states can help prolong its lifespan. |
How do you determine a battery’s State of Health (SoH) and State of Charge (SoC)?
State-of-Charge (SoC) and State-of-Health (SoH) are key quality indicators that provide valuable data for optimizing the algorithms of the BMS. Both parameters are directly related to battery performance and are often mutually confused. SoC is the difference between a fully charged battery and a battery in use, indicating the remaining electricity available in the cell.
QMax: Fully charged.
QAct: Amount of charge it can discharge.
SoC is expressed as the percentage of the remaining charge divided by the maximum charge the battery can deliver. The SoC of a battery can be measured in several ways, which can be categorized for simplicity into two types: Direct and Indirect.
Direct Measures: The SoC can be evaluated directly in several ways.
- Offline Approach: The SoC is determined by fully draining the battery from its current state and measuring the amount of energy.
- Online Method: The SoC is determined by tracking the amount of power that goes in or out of the battery over time. This is known as Coulomb counting. By integrating the current (in Amperes) over time, the total charge can be calculated, helping to determine how much capacity remains in the battery. This technique is commonly used in conjunction with voltage measurements to gauge the battery's SoC accurately.
Indirect Measures: Indirect measures don't measure the SoC directly; they determine it using linked data and various other methods. This group can be broken down further into three types:
- Lookup Table-based Approaches (OCV-SoC Mapping): These methods use Open Circuit Voltage (OCV) and SoC relationships that have already been determined. OCV is the voltage between the battery's connections when it's not giving or getting power.
- Model-Based Approaches (such as Kalman Filters): Model-based approaches use mathematical models of how batteries behave to predict SoC. Techniques such as Kalman Filters use voltage, current, and temperature readings, along with battery models, to accurately determine SoC.
- Approaches based on machine learning (ML): ML techniques, such as neural networks, are used to find complex links between input data (voltage, current, and temperature) and SoC. These models are trained using known SoC values, after which, they are able to predict SoC for new data points.
The choice of method relies on factors such as the importance of accuracy, amount of data, and how it needs to be used. Most battery management systems use more than one of these ways to get an accurate estimate of SoC in various situations.
State of Health (SoH) reflects a battery's overall condition and energy potential. It indicates the amount of potential lifetime energy that has been used and the amount that remains untapped. Monitoring SoH indicates potential issues and the need for replacement. It serves as an early warning system, alerting operators when a battery is nearing its end of life. A battery's capacity drops to around 80%, which typically indicates that it has reached the later stages of its lifespan. Beyond this threshold, capacity loss accelerates, affecting autonomy and performance.
C: Current battery capacity
CBoF: Battery capacity at the beginning of life
What are the components of a BMS?
Typically, a BMS comprises a microcontroller, sensors, and connection wires. Figure 3 illustrates the components of a typical BMS. A microcontroller communicates with cell monitors that monitors the health condition of the cells. This information is used to optimize charging.
Figure 3: Components of BMS (Source: All About Circuits)
Li-ion battery cells must be maintained within specific charge and discharge limits to prevent degradation, typically 15% to 85%. The BMS helps achieve this by providing precise cell measurements throughout the lifecycle of the battery pack. In addition, the BMS manages a complex cell communication, measurement, and analysis system, ensuring optimal operation within the specified range.
What additional functions is a BMS capable of?
A BMS performs additional functions, including:
- Thermal Management: ensures safe operation by monitoring the battery temperature, manages cooling and heating systems, and ensures operation within safe temperature limits.
- Safety Monitoring: detects battery faults and malfunctions, taking action to avoid damage or vehicle damage.
- Overcurrent Protection: monitors the battery pack current and detecting over-safe limits.
- Communication with the Vehicle: communicates with the motor controller and charging system to ensure the safe operation of vehicle systems
Industrial Connectors
Shop our wide variety of Industrial Connectors from TE Connectivity.
Don't forget to join our discussion.
Connecting the components of a BMS
Signal connections in a BMS must be flexible, compact, and vibration-resistant, as well as being able to handle harsh industrial environments. TE Connectivity offers high-voltage cell and module connectivity, switching, and BMS connector solutions that improve power-to-weight ratios, enhance safety, and enable state-of-health monitoring. Their audible locking-system and unique contact design enable efficiency and a long service life, minimizing downtime. Compact yet flexible connector systems support multiple configurations and provide safe creepage and clearance distance between pins, preventing failure from short circuits caused by dust pollution or arcing.
TE Connectivity offers the Dynamic Series connection solutions for high-density, signal, and power control system applications. Dynamic Series connectors include wire-to-board, wire-to-panel, and wire-to-wire housing styles. The D-1000 Series consists of the D-1100, D-1200, and D-1500 series. These ultra-compact connectors conform to UL 94 and USCAR ratings, offering position, voltage, and current ratings, three contact points for high-vibration environments, and various keys for poke yoke, locking, and contact retention.
TE Connectivity's Micro Quadlok System (MQS) is a compact, high-packing, functional contact system suitable for automobiles and various applications. MQS connectors are available in wire-to-wire and wire-to-board versions, with key codings for ergonomic assembly and safe installation. The NanoMQS Portfolio fulfills higher packaging requirements, offering pin counts ranging from 2-16 to medium and high positions on the receptacle side. The NanoMQS connector system reduces PCB footprint by up to 50%.
Summing up: Optimizing the performance of Li-ion batteries
In partnership with
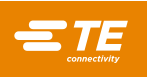
Battery Management Systems are essential for the safe and optimal operation of Li-ion batteries. Li-ion batteries require careful handling to ensure longevity, safety, and optimal performance. Advanced battery management systems combine battery state of charge accuracy, cell balancing, thermal management, and protection against overcharge and discharge, ensuring efficient energy distribution and optimization. TE Connectivity offers a complete lineup of compact and durable connectors capable of interfacing the components that make up a modern BMS.
What tips and tricks do you have for prolonging the lifespan of a lithium-ion battery?
Please tell us in the Comments section below.