An overview of how battery management systems in EVs keep batteries working at their best.
Optimizing Batteries in EVs
A Battery Management System (BMS) actively controls a battery system’s diagnostics and safety functions, which include current monitoring, voltage monitoring, cell balancing, and thermal management. It ensures a battery does not exceed its safe operational limits. By incorporating connectors as part of a BMS platform, the performance and reliability of an EV (electric vehicle) battery can be improved by implementing unique interconnect designs such as Wire-To-Board, FFC/FPC, FPC-to-Board, and Crimp-to-Wire connectors. This article discusses battery management technology utilizing lithium-ion batteries, one of the most efficient battery technologies used for EVs today. It also introduces LV214 Severity-3 and USCAR-2 V2 automotive standards with respect to connectors in a BMS application.
Lithium-ion Batteries
Lithium-ion batteries have several characteristics that make them the preferred power source for many applications. Li-ion batteries have a long battery life expectancy and do not exhibit memory effect, the phenomena where a battery’s longevity is reduced due to incomplete discharge before recharging. Additionally, the specific energy and energy density of Li-ion batteries are very high when compared to other rechargeable battery technologies. Specific energy is the measure of how much energy a battery can store in comparison to its weight, while energy density is the amount of energy that can be stored in a region of space.
Li-ion are well-suited for use in EVs due to their high power-to-weight ratio, high energy efficiency, high-temperature performance, and low self-discharge. Figure 1 compares Li-ion batteries with various other rechargeable battery technologies. Additionally, Li-ion batteries are sealed, and thus, maintenance-free. One significant advantage of Li-Ion battery technology in automotive applications is its safe operation in multi-cell configurations.
Figure 1: Comparison of secondary batteries
Source: A. El Kharbachi, et al., Journal of Alloys and Compounds, Volume 817
Improving the Battery Life Expectancy of Li-ion Batteries
There are several considerations for optimizing the battery life expectancy of Li-ion batteries. Lithium-based batteries are vulnerable to over-voltage. Each cell in multi-cell systems must have an over-voltage detection circuit in order to improve its functional life. Battery performance degrades over time due to cycling, aging, and elevated temperatures. Current and voltage control components, along with temperature control technology are required. The maximum allowable charging current is also dependent on temperature. A controlled charging current is essential for increasing the battery life expectancy of Li-ion batteries.
There are several ways to maintain a good battery life expectancy, including:
- Using partial-discharge cycles
- Avoiding charging to 100% capacity
- Limiting the battery temperature
- Avoiding high charge and discharge currents
- Avoiding deep discharges (below 2 V or 2.5 V)
Interconnects
Shop our wide variety of Interconnect Systems by Amphenol Communications Solutions.
Don't forget to join our discussion.
To create a battery system for an EV, an engineer must take into consideration electrical, mechanical, and thermal design. The system must maintain electrical safety, even under severe conditions, preventing overcharge, over-discharge, overcurrent, overpower, leak current, short circuit, and electric shock. The system must have sufficient mechanical strength and be able to withstand conditions such as shock, vibration, and thermal expansion. A solid interconnect system design is required. The United States Council for Automotive Research (USCAR) USCAR2 performance standard and its European counterpart, LV214, require such connectors to undergo rigorous testing to ensure they are suitable for use in electric vehicles.
What does a Battery Management System do?
A BMS protects the cell from overheating and overcharging by monitoring its voltage and temperature, and limiting its power input and output. In certain situations, the BMS is able to isolate the battery pack from the source and load. Advanced BMS’s are capable of calculating the battery's remaining useful life (RUL), performing cell balancing, and storing historical data. A BMS monitors the lithium-ion battery packs during charging and discharging, and balances the cells within the pack, improving battery life expectancy and capacity.
Figure 2: BMS block diagram
Source: IEEE
Figure 2 depicts a block diagram of a BMS. The temperature, current, and voltage are monitored in real time by sensors installed on the battery pack. These measurements are used to determine parameters, such as state of charge (SoC), state of discharge (SoD), state of health (SoH), as well as charge/discharge capabilities. Cell balancing is performed based on these measurements, as well as actions protecting the battery from overcharging and overheating. The BMS controls electronic components such as current/voltage/leak detectors, disconnect switches, contactors, fuses, and input/output control systems.
State of Charge (SoC)
SoC is defined as the ratio of the currently available capacity of a battery to its rated capacity. An estimation of SoC can be used to determine the battery’s remaining capacity when discharged. One method of estimating SoC is via Coulomb counting, a technique based on the measurement of current, and the integration of that current over time. Coulomb counting yields relative change in SoC, and not absolute SoC. The following equation is used to calculate SoC via Coulomb counting:
Where:
- SoC(t) = estimated State of Charge at time, t
- SoC(t-1) = previous State of Charge at time, t-1
- I(t) = charging or discharging current at time, t
- Qn = battery cell capacity
- Δt = time step between t-1 and t
State of Health (SoH)
SoH is the percentage of the battery’s nominal capacity. Aging and charge-discharge cycles are significant factors that reduce the SoH of a battery. The SoH of an average Li-ion battery is reduced to approximately 80% after 1000 charge-discharge cycles. The commonly used method to determine SoH is with the following equation:
Cell Balancing
The goal of cell balancing is to equalize the voltage on each battery pack cell. Due to manufacturing inaccuracies, the cells in the same battery pack lack equal capacitance or nominal voltage. Cell balancing improves system health and efficiency by monitoring and matching the SoC of each cell.
The Architecture of a BMS
Battery management systems are implemented with either a centralized or decentralized topology. In a centralized system, one BMS monitors, balances, and controls all the cells. There are several types of decentralized systems. In a modular system, the BMS is divided into multiple, identical modules, with one designated as the leader. The leader controls the system, while the other modules act as remote measuring devices. In a distributed system, the boards that house the electronics of the BMS are installed on the cells being measured.
A BMS system in an EV uses a wide variety of interconnects and cabling, the choices of which depend on power and signal requirements. These advanced control systems ensure that the battery and vehicle systems are safe, highly efficient, reliable, and have a long battery life expectancy.
Amphenol Compact Automotive Electrical Connectors
The automotive BMS's accuracy, performance, reliability, and maintenance of safety standards are directly related to the components used within the system. A reliable and durable interconnect solution is one of the most important considerations. Amphenol offers a wide range of compact, flexible high, performing automotive-grade connectors for EV Battery Management Systems design, including compact connectors that satisfy the growing demand for miniaturization in the automotive application market. WireLock® 1.8mm, Minitek Microspace, and Flexlock FFC/FPC connectors are well-suited for use in automotive battery management systems.
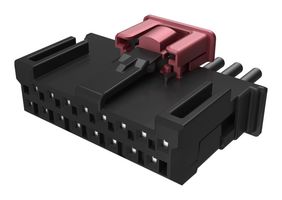
Minitek MicroSpace 10142348 Series
Buy Now
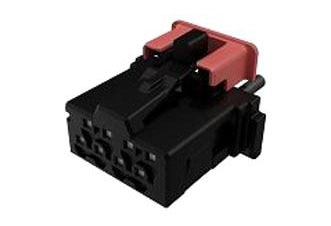
Minitek MicroSpaceXS 10155504 Series
Buy Now
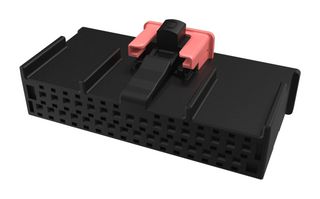
WireLock Connector Housing 32 Positions
Buy Now
Summing Up: Managing Modern Battery Systems
in partnership with
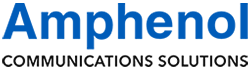
As battery systems become more complex, battery management systems are being employed to increase performance, reliability, and battery life expectancy. A BMS keeps a watchful eye on lithium-ion battery packs and their charging cycles, and balances the cells within the battery pack. With a reliable BMS system, damage due to overcharging and overhearing is minimized, and the useful lifetime of the battery is maximized. For durable and reliable connections within the battery system, Amphenol offers a range of compact automotive-grade connectors that comply with US and European performance standards for automotive electrical connector systems.
Click here for more information about EV Charging.
Glossary
Battery (Pack) - One or more cells that provide the specified operating voltage and current
Battery Cycle Life - also known as Battery Life Expectancy. The number of charge/discharge cycles that a battery can undergo before its nominal capacity falls to 60%-80% of its initial capacity, and considered end of life (EOL).
Capacity – the quantity of energy, expressed in amp-hours that can be delivered by a battery
Cell – the basic unit that provides electrical energy by conversion of chemical energy. A cell consists of an electrolyte, container, electrodes, and electrical terminals
Charging – the process of providing electrical energy to a rechargeable battery or cell
Discharge – the release of energy from the cell or battery
Energy Density – the energy in a battery or cell expressed in terms of its size
Memory Effect – The loss of capacity due to an incomplete discharge before charging
Overcharge – Charging after the maximum, safe capacity of a battery has already been reached
Self-Discharge Rate – the rate of energy loss during extended storage due to internal chemical reactions
Specific energy - the measure of how much energy a battery can store in comparison to its weight
EVs are getting a range of ~200 miles. What do you think will be the maximum range in 5 years, and what are the advancements that will make that happen?
Please tell us in the Comments section below.