An introduction to remote monitoring in IIoT and its benefits in safety and efficiency.
sponsored by
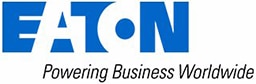
How are industrial applications monitored?
The proliferation of Industry 4.0 brings many advancements, including real-time monitoring and control. With improvements in communications technologies and cloud computing, as well as advancements in sensors, robotics, and motor control, Information Technology (IT) and Operations Technology (OT) become more tightly integrated. This enables unprecedented control over the manufacturing process and related operations. Monitoring can be done remotely, allowing equipment to be observed and controlled from a safe distance. Many systems are web-enabled, transforming smartphones and laptops into HMIs (human machine interface) for industrial systems.
Remote monitoring and control via IoT
Monitoring systems typically display information from intelligent devices, such as protective relays, meters, programmable logic controllers (PLCs), and remote terminal units. Traditionally, systems like this have been supervisory control and data acquisition (SCADA) systems that are custom-built specifically for the system. Developing and field testing a custom system can take a great deal of time. Programming frequently takes multiple iterations before all the necessary functionality is provided. Once completed, a monitoring system can be used to detect anomalies and prevent failures before they occur.
To address the long development time of building a custom monitoring system, electrical equipment manufacturers have created application specific processors that can be housed in low or medium voltage electrical equipment. The processor communicates with all of the electronic devices connected to it, displaying relevant data on a dashboard user interface. The configuration of the processor and electronic devices can be done at the factory, along with testing. Such systems are typically web-enabled and thus, require strong security features, such as Role-based Access Control (RBAC) password management and Secure Sockets Layer (SSL) encryption.
A significant benefit of remote monitoring is safety. One of the most dangerous hazards affecting electrical systems is arc flash, a sudden and unexpected discharge or explosion that can generate large amounts of thermal heat, toxic fumes, pressure waves, and blinding light. The most effective way to limit injury due to an arc flash event is removing operators from the hazard area. Traditionally, a mimic panel, wired with control switches and indicator lights, is built, enabling circuit breaker operation outside of the arc flash boundary.
A modern and more effective way of remote operation is to use a processor installed in the electrical equipment, which connects to an HMI outside the arc flash boundary. Circuit breakers can be operated through the HMI. Connecting the HMI to the processor requires only one Ethernet cable, which greatly reduces the complexity of the build, when compared to a traditional mimic panel. Figure 1 illustrates the operating of circuit breakers via HMI.
Fig: 1 Dashboard – remote circuit breaker operation
Source: Eaton
An equipment monitoring system enables IoT-based, real-time data collection and analysis. A typical monitoring system consists of the following components:
Fig 2: Web-based remote equipment monitoring system
- Factory equipment – Sensors are mounted on the factory floor to measure physical characteristics such as temperature and vibration.
- Server or Cloud - The data from the sensors is sent to a central computer or cloud for analysis. Data can be formatted for visualization as well as analyzed with ML for predictive maintenance purposes.
- User Interface - Mobile and web applications enable users (e.g., operators and technicians) to communicate with the system and view real-time data and reports based on business logic.
Big Data Analytics for Industry 4.0
The sensors installed in IIoT systems generate vast amounts of data, which can be used to enable predictive maintenance (PdM). The goal of a PdM system is to predict when maintenance is needed based on analysis of historical data, including the equipment’s running temperature, sounds, vibrations and more. Machine learning (ML) is used to study the large amounts of data, searching for patterns within it that might indicate required maintenance or repair. The more data there is, the more accurate predictions will be.
PdM has several advantages over preventative maintenance. With preventative maintenance, parts are replaced at fixed intervals, based on manufacturer suggestions for the parts’ service life. Industrial parts often have an actual service life far greater than the manufacturer’s suggested service life. Replacing a part sooner than necessary increases costs. Additionally, industrial systems often must be shut down for maintenance. With PdM, maintenance is performed only when needed, reducing the overall number of system shutdowns.
PdM typically relies on cloud computing for its intensive data analysis. HMIs often have data visualization features, enabling users to customize the models generated by ML.
Figure 3 depicts a diagram of the business solution from the Brightlayer Data Centers, Eaton’s software suite, which includes infrastructure management, 3D visualizations, cloud-based analytics to support PdM.
Fig 3: Brightlayer Data Center Suite
Source: Eaton
Energy Savings and Efficiency
The availability of real-time monitoring and data analytics also brings an important benefit: energy savings and efficiency. Energy monitoring and visualization shine a light on wasteful habits that should be modified, and intelligent control of lights and other equipment enable automatic adjustments based on usage. According to the U.S. Department of Energy, savings from digitalization of building infrastructure could lead to an estimated $126 billion in energy costs and 841 million metric tons of carbon emissions.
In order to reduce energy consumption and combat climate change, several energy standards have been adopted across the United States, including:
- ASHRAE 90.1 - The American Society of Heating, Refrigerating and Air-Conditioning Engineers (ASHRAE) 90.1 specifies the minimum standard for energy-efficient design in buildings. It includes specifications for HVAC and lighting systems, as well as construction.
- CEC Title 24 – The California Energy Commission’s (CEC) Title 24 is a code of standards for residential and non-residential buildings throughout California. Title 24 covers “energy conservation, green design, construction and maintenance, fire and life safety, and accessibility.” This energy standard aims to promote energy efficiency in new homes and commercial establishments.
- Local Law 97 – Local Law 97 is a groundbreaking law that requires that most NYC buildings over 25,000 square feet meet new greenhouse gas emissions limits and energy efficiency by 2030. It aims to cut the emissions generated by the city's biggest buildings by 40 percent by 2030 and 80 percent by 2050
The above energy codes affect electrical systems that support lighting, heating, ventilation, air conditioning (HVAC), and plug loads that account for a significant portion of building energy consumption.
Eaton Power Xpert Dashboard
Power Xpert Dashboard is a comprehensive interface to control Eaton’s wide variety of switchgear, motor control centers, switchboards, and panelboards. Featuring a multi-touch touchscreen HMI, users can monitor and control devices remotely, from a safe location outside the arc flash boundary. Power Xpert Dashboard also supports PdM, improving system uptime. The software can be custom configured at the factory for specific systems, simplifying installation, use, and maintenance.
Fig 4: Power Xpert Dashboard
Source: Eaton
Eaton PowerXL Series DG1 VFDs
Power Xpert Dashboard can be used to monitor and control the PowerXL series of variable frequency drives (VFDs). The PowerXL series is designed to reduce energy consumption, improve safety, and support reliable operations for the heating, ventilation, air conditioning and refrigeration (HVAC/R) market.
Fig 5: PowerXL DG1 Series Variable Frequency Drives
Buy Now
The PowerXL Series DG1 VFDs is a general purpose drive that incorporates a patented energy control algorithm, extensive onboard industrial communication protocols and HVAC-tailored hardware, firmware, and communications.
Summing up: monitoring and controlling equipment remotely
The connectivity of the IIoT enables equipment to communicate with each other and the cloud, bringing advantages such as remote control and monitoring. Engineers can now configure and monitor equipment at a safe distance from the potentially dangerous factory floor. Additionally, the data generated from the sensors monitoring the equipment can be analyzed to build models for predictive maintenance. Eaton’s Power Xpert Dashboard software suite brings remote monitoring and control to the company’s wide range of switchgear, motor control centers, switchboards, and panelboards. Power Xpert Dashboard can be custom configured at the factory, reducing install time and compatibility problems.
For more information on modern control algorithms for VFDs, check out our Essentials on the Basics of Motor and Drive Efficiency.
What types of applications could benefit the most from remote monitoring?
Please tell us in the Comments section below.