As devices become smaller, the size of the connectors inside become increasingly important.
Electronics are Becoming Smaller
Miniaturization has become increasingly important in the electronics industry. Compact and efficient electronic devices are in high demand, and designers are under pressure to create products that are smaller, but still deliver superior performance. Manufacturers are required to fit parts into even tighter spaces. This is particularly true for modern, advanced products that use various multi-board assemblies. Achieving miniaturization in board-to-board connectors remains a significant challenge. This article takes a look into the latest trends and challenges related to developing miniaturization, with a particular focus on the innovative Molex Quad-Row connectors.
What are the Challenges of Miniaturization?
In most electronic devices, the largest components are the connectors and cables. Thus, it is important to miniaturize connectors to attain form factor targets, enabling greater input/output (I/O) and feature density. Miniaturization is especially desired in applications such as RF/wireless devices, smart consumer devices, data center infrastructure, and edge computing. Beyond semiconductor scaling, there are many factors driving the trend toward smaller, slimmer, and more streamlined designs:
- More features, made possible by the increased the number of components packed into a smaller board or enclosure space as well as the enhanced capabilities of installed chips.
- Greater I/O density to support the greater feature requirements.
- User experience evolution that drives the demand for different device form factors, which then spur new miniaturization requirements.
The process of miniaturizing connectors presents numerous challenges, including maintaining signal integrity, ensuring mechanical durability, managing manufacturing tolerances, power handling, thermal management, and dealing with connector mating and un-mating forces. Additional challenges of miniaturization include:
- The smaller the connector, the more challenging it is to assemble.
- As terminal pitch narrows, it becomes much more difficult to manage EMI.
- With smaller contact areas, impedance matching between the board and connector is challenging.
- Smaller connectors tend to be much more delicate.
Connectors need to be mechanically robust to withstand challenging conditions (mechanical forces, solder rise, corrosion, coplanarity) on the assembly line and in use. Additionally, their design must be as future-proofed as possible, supporting new functions and capabilities when they are added.
Connector Miniaturization in Key Markets
As technology advances, the I/O capabilities and feature density of applications such as smart consumer devices and edge computing become higher. To keep devices compact and portable, many of the parts within an assembly must be miniaturized. Examples of miniaturized connectors found in key markets include:
RF and Wireless Systems
In general, coaxial connectors are used to transfer signals in the 5G frequency range; however, coaxial cables and cable assemblies are bulky and the compact form factor of the typical handset leaves no room for them. Surface mount board-to-board connectors allow the stacking of components or connection to a flex ribbon cable. Additionally, smaller connectors require smaller PCB lands, which leaves room for other components, such as batteries or memory. Landing pad pitches in mmWave systems are typically below 0.5mm; this helps to prevent dielectric absorption in the PCB substrate, one of the factors in signal loss. Additionally, leveraging printed RF circuits and integrating larger, more densely packed antenna arrays help to create highly efficient wireless systems and deliver more advanced functionality.
Consumer Electronics
Consumer electronic products, such as smartphones and tablets, often feature slim and compact designs that require the miniaturization of key components. To fit into the thin housings of these devices, the mating connectors that connect display modules or antennas to the main PCB must be extremely small. These connectors facilitate power and signal transfer and must support high current ratings, as well as maintaining signal integrity for high frequency digital signals.
Data Center and Edge Computing
In specialized computing paradigms such as edge AI, connector systems play an important role in enabling high-speed data transfer and delivering power between components on the motherboard, peripherals, and external equipment. The goal of edge computing is to provide data center capabilities in a smaller form factor closer to end users. Miniaturization of internal components enables edge devices to meet size requirements.
Connectors
Shop our wide variety of Quad-Row Connectors from Molex.
Don't forget to join our discussion.
Automotive
Miniaturization enables the integration of multiple electronic functions in a vehicle into a single compact module, reducing the complexity and cost of the overall system while increasing reliability and performance. Complex systems, such as advanced driver assistance systems (ADAS) and autonomous driving systems, require a high level of integration and miniaturization. Additionally, miniaturization enables manufacturers to reduce the overall size and weight of electronic components, making vehicles more fuel-efficient and eco-friendly. Miniaturized components can help to enhance the aesthetics of the vehicle's interior design, giving manufacturers more freedom in creating sleek and modern designs.
Medical Devices
In the past, healthcare devices were large and complicated, requiring patients to remain stationary while measurements were begin taken. Modern medical devices are portable and can be worn discreetly by patients during their daily activities. Nowadays, smartwatches, phones, and other wearable devices can measure a wide range of health parameters such as blood oxygen levels, respiratory rate, heart rate and rhythm, sleep quality, and wrist temperature. This progress has spurred medical-grade device manufacturers to strive for smaller, less intrusive, and easier-to-handle patient-monitoring devices.
Molex Quad-Row Connectors
Molex Quad-Row board-to-board connectors are the smallest board-to-board connectors available, thanks to their unique staggered-circuit layout, which offers a space-saving advantage of up to 30%. Molex Quad-Row connectors are designed to support the demands of space-constrained applications, including smartphones, smartwatches, wearables, game consoles, and AR/VR devices. Figure 1 depicts the receptacle and plug of a Quad-Row connector.
Figure 1: Quad-Row Connector Structure (Receptacle and Plug)
Source: Molex
Molex Quad-Row connectors have insert-molded fitting nails and interior armor to ensure durability and reliability during high volume manufacturing and assembly. These protective measures safeguard the pins from damage, preventing problems that may typically arise during production. In addition, the wide alignment design of these connectors makes mating easy and secure, reducing fallout rates. Molex Quad-Row board-to-board connectors achieve a 0.175mm signal pitch, while retaining the industry standard 0.35mm soldering pitch. This makes them compatible with typical surface mount manufacturing processes, streamlining volume manufacturing. In terms of electrical capabilities, Quad-Row connectors have a maximum current rating of 3.0 A, allowing for high-power applications within a compact form factor.
Figure 2: Quad-Row Connector Pitch Spacing
Quad-Row board-to-board connectors are available in two sizes with either 32 or 36 pins. 20 and 64-pin options will be available soon, with plans to support up to 100 pins.
How is a Smart Watch made?
Figure 3: Construction of a Smart Watch
Most wearable devices have a very small form factor, and a smart watch is no exception. The assembly of a smart watch seems like an incredible feat considering the number of tiny components within. A typical smart watch includes:
- Main processor: The "brain" of the smartwatch, running the operating system and other software
- Display: Typically an OLED or LCD screen, used to display information and interact with the user
- Sensors: A variety of sensors, such as heart rate monitor, accelerometer, gyroscope, GPS, ambient light sensor, and more
- Battery: Smartwatches typically use a small rechargeable battery to power the device.
- Wireless communication: Wi-Fi, Bluetooth, NFC, and cellular connectivity to allow the smart watch to communicate with other devices
- Memory and storage: Smartwatches have varying amounts of memory and storage to store data and run apps.
- Input/output: Components such as buttons, touchscreens, microphones, and speakers to allow the user to interact with the device
Additionally, board-to-board connectors, such as Molex’s Quad-Row connectors, are used to connect the PCB to the various components.
The assembly of a smart watch is an automated process; the surface mount components are soldered to the PCB in a process called reflow soldering. In this process, a solder paste is applied to the PCB pads using a stencil. The components are then placed onto the PCB using a pick-and-place machine. Because the parts are so small, specialized microscopes and computer vision are often employed to ensure the correct positioning and alignment of each component. The PCB is then heated in a reflow oven, which melts the solder paste and fuses the components to the PCB. The oven temperature is carefully controlled to prevent damage to the components and the PCB. After soldering is complete, the PCB is inspected for defects, such as solder bridges, insufficient solder, or misaligned components. This process is highly automated and can be done at a high rate of speed with minimal errors.
Summing up: How are Tiny Devices made?
in partnership with
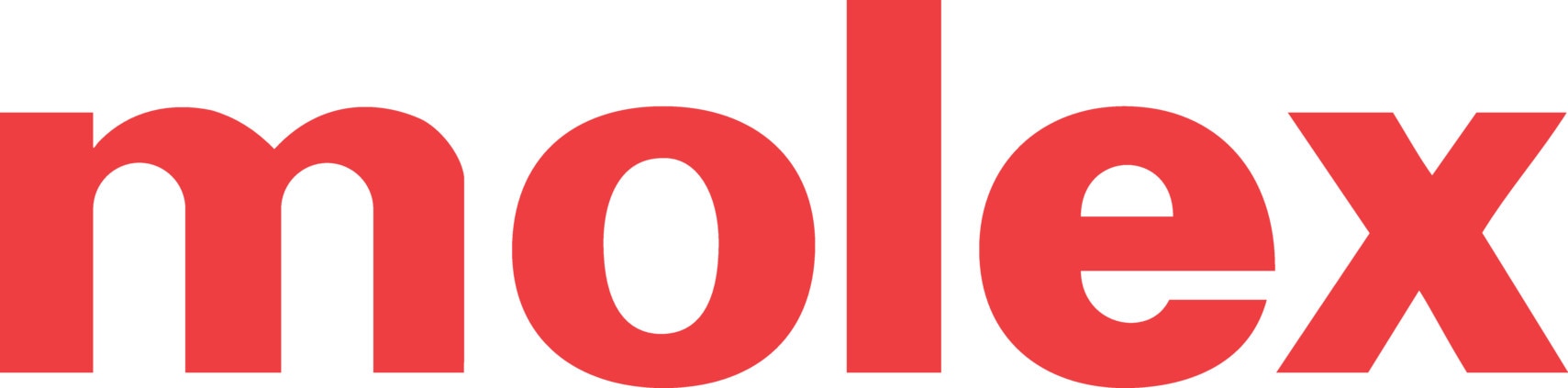
Advancements in technology has led to the miniaturization of almost every type of product. It was only in recent times that an entire computer could fit in the palm of your hand. As devices get smaller, as do their internal components, some of the largest being connectors. Connectors, such as the Quad-Row board-to-board connector from Molex, have an incredibly small form factor, which has enabled the development of even more compact devices, such as smartphones, tablets, and wearables.
What are some of the smallest devices you've built?
Please tell us in the Comments section below.