Sensors Series - Part 6 - Automotive for EV/HEV
The automobile industry plays a significant role in global economic growth, and the electrification of the car has created new challenges in hybrid electric vehicle (HEV) and fully electric vehicle (EV) design. As per International Energy Agency forecasts, an estimated 250 million EVs and HEVs will drive on the world’s roads by 2030. EVs positively impact the power system and environment, with limited sensor populations, greenhouse gas reduction, and miniaturized components. The technology continues to evolve as automotive power units. This learning module reviews the essential parts used in HEVs and discusses the range of technology, from the internal combustion engine (ICE) to fully electric vehicles (EVs).
Related Components | Test Your Knowledge
sponsored by
2. Objectives
Upon completion of this module, you will be able to:
- Define the importance of automotive sensors and why they are needed
- Describe the transition in vehicles from a conventional internal combustion engine (ICE) to an electric motor
- Explain the architectures of EVs / HEVs along with their advantages
- Discuss the different sensor technologies used in battery-powered electric vehicles
3. Scope
The transportation industry accounts for 25%–30% of total greenhouse gas emissions. The fuel combustion of an ICE produces various gases like CO2, NO2, NO, and CO. These gases cause the greenhouse effect and adversely affect human health. The transportation industry has come up with alternative solutions: hybrid electric and fully electric vehicles. These vehicles produce better performance compared to ICEs. We will discuss various automotive sensors (position, speed, temperature, and pressure) required for EV and HEV operation.
4. Basic Concepts
ICEs are thermally inefficient, with most gasoline combustion engines operating at 20 percent thermal efficiency as most of the fuels' energy turns into waste heat. The global promotion of environment-friendly CO2 reduction initiatives and the adoption of regulatory compliance introduced battery-powered electric vehicles (EV) and hybrid electric vehicles (HEV). These two technologies are environmentally-friendly alternatives. It has also helped that the new Dynamic Force Engine revolutionized the automotive industry, as it is 40 percent more efficient compared to conventional engines.
- 4.1 Basic Architecture of HEVs/EVs
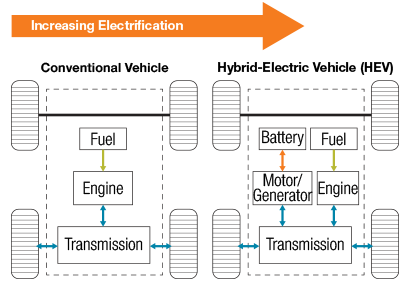
Figure 1: Basic working of different types of vehicles [Source: IEEE Overview of Electric Vehicles (EVs) and EV Sensors]
These components are classified into three groups:
- Drivetrain, which physically integrates the ICE power source and electric drive.
- Battery/energy storage system (ESS), which provides energy storage and power capabilities.
- Control system instructs the electric systems/ICE and manages the hybrid ESS.
These components are integrated using multiple methods and sizes, which leads to innovations in vehicle design.
- 4.2 Working Principles of EVs/HEVs
The Technical Committee (Electric Road Vehicles) of the International Electrotechnical Commission describes an HEV as a vehicle in which propulsion energy is extracted from two or more energy sources. At least one of them delivers electrical power. The EV operates with electricity stored in batteries, fuel cells (FCs), and ultra-capacitors (UCs), where the eventual electricity source includes renewable energy resources and power generation plants. EVs are a significant contributor to this new power system of advanced grid systems and renewable generating facilities. The hybrid/electrical control unit is the powertrain's brain, and it controls the power distribution, energy storage, engine, and motor. The unit enhances EV powertrain efficiency.
Battery electric vehicles colloquially referred to as EVs are equipped with rechargeable batteries that run all onboard electronics and the electric motor. Contemporary HEVs run on power generated by a combination of ICE and single or multiple electric motor(s) that use battery-stored energy. HEVs combine the benefits of low tailpipe emissions and high fuel economy with conventional vehicles' range and power.
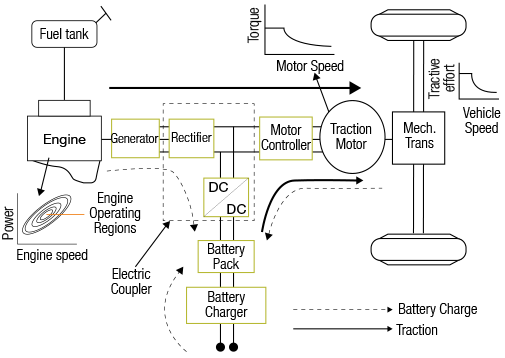
Figure 2: Detailed Configuration of a Series Hybrid Vehicle [Source: NPTEL – Electrical Engineering – Introduction to Hybrid and Electric Vehicles]
Figure 2 shows a hybrid-electric vehicle where an electric motor is one source of power. The other motive power source is typically offered by an ICE engineered to run on either diesel fuel or gasoline. In most cases, the HEV propulsion force is provided by a combination of an electric motor and an ICE.
- 4.3 EV Classifications
EV chargers are differentiated by the speed with which they recharge EV batteries. The Society of Automotive Engineers (SAE) describes three distinct charging stations levels, aka electric vehicle supply equipment (EVSE):
The classifications comprise Level 1, Level 2, and Level 3 (DC fast charging). In Level 1, a standard household (120v) outlet (12 - 16A, 1.0 to 1.5 kW) plugs into the electric vehicle. It takes about 8 hours to charge a Level 1 EV for approximately 75-80 miles. The charging is generally done at home or in the workplace. These chargers can charge a majority of commercial EVs.
Level 2 charging needs a specialized station that pipes power at 240v (15A-80A, 7 – 9 kW). Level 2 chargers are generally available at public charging stations and workplaces. About 4 hours are needed to charge a battery for 75-80 miles of range.
Level 3 charging, aka DC, or fast charging, is currently the quickest charging EV market solution. They supply anywhere from 300V up to ~920V at a maximum of ~500A, 50 kW. Level 3 chargers are found at exclusive EV charging stations and charge a battery for 90 miles range in about 30 minutes.
- 4.4 Advantages of Electric Motor Vehicles Over Internal Combustion Engine Vehicles
In terms of emissions, the electric car rates better than its combustion engine counterpart, in that it generates zero tailpipe emissions. Another advantage to the EV is minimal traffic noise, as the EV motor runs noticeably quieter. Yet another significant advantage of any full electric-powered vehicle is its considerably lower consumption cost. Moreover, the EVs price and kWh consumption make a significant positive difference compared with any ICE vehicle's consumption.
The electric engine consists of minimal moving parts, and there is no requirement for oil, radiator coolant, water change, or engine starting sparks. Reduced engine components improves reliability and lowers vehicle maintenance costs. The engine's instant torque is another positive, as it offers maximum power from a stationary position. An ICE, in contrast, can only accomplish the same at high speed. The power delivery is undeniably smooth and achievable at any moment during the drive. The cost factor of purchasing any new EV must be noted as subsidized by the government, stimulating public interest to purchase EVs over conventional automobiles.
- 4.5 Sensors in EV/HEV Design
EV/HEVs require various sensors to fulfill crucial tasks like passenger comfort, engine performance, and vehicle dynamic behavior. Sensors are essential contributors to vehicle performance, image, customer appeal, and quality. The HEV & EV sensor market is particularly keen on safety and control, and this application has almost doubled its value in five years. We will discuss more on different types of sensors available for EVs/HEVs in our next section.
5. Analysis
Electric vehicle batteries are designed to meet two vital requirements: they must be long-lasting energy systems, and also be high power systems. In other words, batteries for EVs and HEVs have to provide high voltage and high current. These make a battery management system for EVs much more complicated than those for portable electronics.
Engines are absent in battery-powered EVs. An electric vehicle requires a single or two positions and speed sensors, while an HEV needs more position, speed, pressure, and temperature sensors.
Electric vehicles are powered by substantial battery banks, constructed of extended strings of batteries in series. Many manufacturers have turned to lithium-ion batteries, such as lithium-titanate, lithium-phosphate, and lithium-manganese for electric vehicles in search of higher energy-efficiency. Optimal and safe use of these batteries requires a battery management system (BMS), which includes a battery monitor and controls power storage systems, assures the health of battery cells, and delivers power to vehicle systems.
- 5.1 Sensor Solutions for EVs/HEVs
Amphenol Sensors offers a sensor portfolio of off-the-shelf and customized products for regulatory and industry-driven EV and HEV applications. Figure 3 describes the various sensing solutions that help automotive manufacturers design vehicle electrification systems.
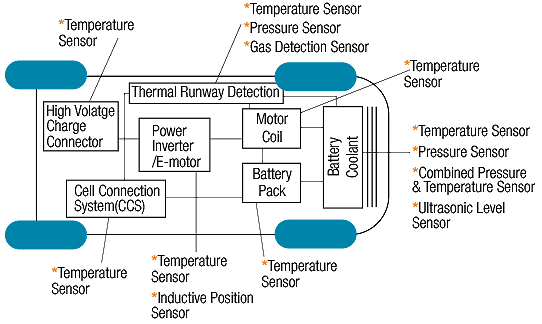
Figure 3: Sensors for EV/HEV Applications [Source: Amphenol]
Major Markets Served | Thermometrics, Inc. Temperature | Telaire Gas & Moisture | NovaSensor Pressure | SGX Sensortech Gas | Piher Sensing Systems Position | I2S Pressure & Temperature | SSI Technologies Ultrasonic Level & Quality |
---|---|---|---|---|---|---|---|
EV/HEV | Yes | Yes | Yes | Yes | Yes | Yes | Yes |
Battery Coolant | Yes | - | Yes | - | - | Yes | Yes |
Battery Pack | Yes | - | - | - | - | - | - |
Cell Connection System (CCS) | Yes | - | - | - | - | - | - |
Charger Connector | Yes | - | - | - | - | - | - |
Motor Coil | Yes | - | - | - | - | - | - |
Power Inverter / E-Motor | Yes | - | - | - | Yes | - | - |
Thermal Runaway | Yes | Yes | Yes | Yes | - | - | - |
Table 1: Sensing Technologies Source: Amphenol
A Battery Pack is a collection of individual batteries that serve as the vehicle's primary fuel source, substituting hydrocarbon fuels in ICE automobiles. Thermal runaway Detection occurs when battery cells exceed allowed operating temperature, leading to an explosion or fire, which can then proliferate to other cells within the battery pack. A Cell Connection System (CCS) used as a battery cell top cover connects with the BMS. A Power Inverter / E-Motor powers the electric motor by converting any higher voltage DC electricity to a lower voltage AC electricity. The vehicle battery is charged through a high voltage source linked with a High Voltage Charger Connector. Optimum battery temperature is maintained using Battery Coolant. The Motor Coil Wire coils conduct electric current and generates a magnetic field. The two interact with rotating the motor shaft, and electrical energy is converted to mechanical energy.
- 5.1.1 Battery Coolant Sensors
An effective cooling system poses a challenge for battery engineering. Battery discharge in electric cars generates heat. Since batteries are designed to work within defined temperature extremes, an absent cooling system pauses work. An EV battery cooling system has the following attributes: temperature range and uniformity, ease of use, energy efficiency, size, and weight.
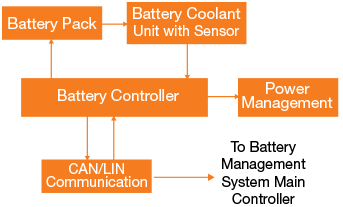
Figure 4: Block Diagram of Battery Coolant Temperature Sensor
The battery coolant section comprises a temperature sensor, which measures and monitors the inlet/outlet battery coolant's fluid temperature to indicate battery cell temperature, as well as a pressure sensor that measures the cooling system pressure to control pump capacity. The combination of both sensors helps optimal thermal management. The Ultrasonic level sensor continuously monitors the fluid level to detect coolant leakage during its nascent stage.
Amphenol Thermometrics' Coolant Leak Detection Sensor uses variation in sensor resistance values to detect coolant leakage, and a signal is sent to the BMS to warn the driver. The alert pushes the operator to execute remedial measures to minimize pack failure risk and electricity-related hazards.
A Thermometrics Coolant Temperature Sensor (CTS) reviews the coolant temperature. The coolant circulates in the battery to cool the EV’s/PHEV’s battery module. The CTS relays a signal to the BMS if the battery module overheats. The latter harnesses information to protect battery packs from any damage and to maximize performance. The water temperature sensor monitors the coolant circulating in the engine block to cool the engine. This sensor warns the vehicle driver of the engine overheating. The driver then stops the vehicle, and the engine is switched off to prevent permanent damage.
- 5.1.2 Battery Pack Sensors
A battery pack contains a temperature sensor to measure and track the battery cell's multiple batteries' surface temperature. Knowing the surface temperature is vital to preserving battery chemistry. Longer-term battery performance requires reliable and accurate temperature sensing measures. Amphenol produces an NTC thermistor and other highly precise temperature solutions with performance standard high stability.
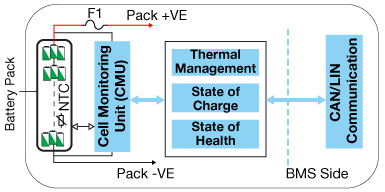
Figure 5: Battery Pack Block Diagram
An EV battery pack comes with cell modules and a thermal management system where a module interconnects the power management and thermal management systems. Different kinds of cooling systems influence battery pack thermal management system performance. The heat transfer medium can be air, liquid, heat pipe, phase change material (PCM), or a combination of these. The Battery Pack Temperature Sensor is essentially a ring terminal temperature sensor tasked to measure surface temperature. The temperature on hybrid batteries is reviewed for overcharging protection and for optimizing battery performance. The Type FL Low Profile NTC Temperature Sensor contains an NTC chip thermistor enclosed within a flat flexible circuit (FFC) covered by a thin-film protective coating. With its contour conforming flexibility and low profile (1.0 mm max thickness), this sensor is ideal for EV/HEV Battery Pack Temperature sensing.
- 5.1.3 Cell Connection and Cell Balancing Systems
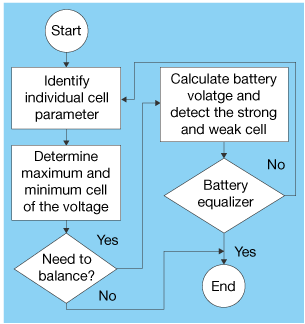
Figure 6: Flowchart of Cell Balancing [Source: IEEE Paper Titled "Battery Cell Balancing Optimisation for Battery Management System"]
The Cell Balancing system offers voltage and temperature sensing to review battery cells' state of charge (SOC). It supports a high current circuit for battery cell connectivity. Cell balancing equalizes voltages and SOC among the fully charged cells. All cells are unique, with slight SOC differences, temperature, self-discharge rate, capacity, and impedance characteristics. Cell balancing helps design a bigger capacity battery for an application, as balancing permits the battery to attain a higher SOC.
Cells are parallel wired in HEVs and EVs to create a high capacity block, and multiple blocks (or cells) are series-connected to generate high voltage. Since each cell is distinct, the cells in a series enjoy identical current but different voltage. Capacity fade in cells during the charging process may be dangerous if a cell easily jumps to its full charge. Similarly, the weakest cell may over-discharge, and it will fail before the others during discharge. When the battery contains multi-cells in series, it may suffer a higher failure rate than any single cell, due to a series network. This effect must be minimized to preserve battery life. An effective cell balancing mechanism to keep SOC levels of independent cells in a battery pack as near to each other as possible must be developed.
- 5.1.4 High Voltage Sensor Charger Connector
This temperature sensor is located inside the connector, and detects over-temperature conditions during charge. The Charge Coupler Connector with Cable can be integrated into Electric Vehicle Supply Equipment (EVSE) for EVs and HEVs. Amphenol offers customers GB Charge Plug and Inlet Series solutions. Amphenol ICC provides customized chargers or battery connectors and terminals that meet general industry standards. These robust and reliable interconnection systems feature better durability.
The Amphenol proprietary Excel|mate CC – IEC Combo meets the IEC 62196-2 Standard for charging systems. The Vehicle Inlet can be used to charge the EV with AC and DC power. The Combo Plug (includes 2 DC power contacts) enables quick charging in public areas. A temperature sensor and a colored LED-equipped Vehicle Inlet and Combo Plug help to monitor the charging status. The Excel|mate CC IEC Combo is available for 60, 125, and 200 A in any required cable length.
- 5.1.5 Motor Coil
The Motor coil temperature sensor, interlaced into motor windings, measures and monitors motor coil temperature to provide feedback on electric motor operating conditions. The bus bar coil or bus bar increases during instances of excessive load or electric motor stalls. This rise in current generates heat in the system, which is then measured by the sensor. Understanding temperature conditions is critical to prevent the system from being damaged. Thermometrics A1737 Motor Coil Temperature Sensor is fitted on a starter generator to offer the motor coil's temperature measurement. It is generally mounted on a neutral bar and detects spurts in current that indicate a failure, leading to a stall. The sensor may also be used to supervise the motor windings’ temperature and warn of any over-temperature conditions.
- 5.1.6 Power Inverter (e-motor)
The motor is the "heart" of any EV, and motor control algorithms need position information for their proper function. The control loop extracts feedback from the position sensor to control the current flow quantum into each motor phase. Such current control is achieved by driving the IGBTs in each phase. Each phase is independently controlled, so that the desired current can be channelled into the motor, generating the torque required to drive the vehicle. In other words, the drive motor that functions as the heart of the electric vehicle must be controlled by a rotatory position sensor. The EV will efficiently consume power if the motor is controlled as per driving conditions. The motor must be thus detected, and its rotational speed accurately reported.
A Power inverter/E-motor temperature sensor computes and tracks the power inverter's operating temperature to offer feedback on high-risk conditions. The inductive position sensor yields data on the rotating motor shaft's angular position for optimized motor inverter control. The Inverter turns higher voltage DC electricity into the lower voltage AC electricity needed to power the electric motor. Hybrid/electric vehicle powertrain systems typically use High Speed Inductive to feedback the rotor shaft's angular position, direction, and speed for optimized motor inverter control. The absolute angle measurement offers instant feedback of the metallic target's angular position with a 12-bit maximum resolution.
- 5.1.7 Thermal Runaway
Thermal Runaway occurs when battery cells exceed allowable operating temperature, potentially causing an explosion or fire, which then propagates to the other cells within the battery pack. Battery cells, especially lithium cells, are susceptible to overcharges and over-discharges. This leads to thermal runaway when the rate of internal heat generation exceeds the heat release rate.
Thermal runaway of single cells within a large-scale lithium-ion battery is a known risk that may devolve to critical situations if no countermeasures are adopted. Faulty cells undergoing thermal runaway within the battery must be quickly and reliably detected for foolproof passenger safety. Sensor selection is based on determining cell thermal runaway impact.
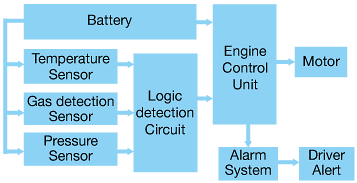
Figure 10: Battery Vehicle Thermal Runway Management System
Temperature sensors measure and monitor battery temperature to detect Thermal Runaway conditions. Single cells or multiple cells can be detected. Pressure Sensors Detect pressure change within the battery cell having Thermal Runaway conditions. They are available in Simple 3-command I2C interfaces with minimal current consumption of <35μA.
Gas detection sensors detect Carbon Dioxide (CO2) outgassing to indicate pre-combustion conditions. They are available in single and dual-channel configurations and can be self-calibrated with proprietary ABC Logic Software. These sensors detect combustible gases implying Thermal Runaway conditions, and they are sensitive to multiple gases like H2 / CH4 / CO2.
6. Glossary
- AC (Alternating Current): an electric current that periodically reverses direction and varies its magnitude continuously with time. Direct current, in contrast, flows only in one direction.
- BMS (Battery Management System): a particular electronic system that administers a rechargeable battery (single cell or battery pack) by tracking its state, calculating secondary data, reporting that data, safeguarding the battery, supervising its environment, and balancing it.
- DC (Direct Current): a uni-directional electric current. The flow of charge is always in the same direction.
- EM (Electric Motor): an electrical machine that converts electrical energy into mechanical energy. Most electric motors work through the interaction between the motor's magnetic field and electric current in a wire winding to produce torque (a form of force) applied on the motor's shaft.
- ESS (Energy Storage System): equipment that can store safely, efficiently, and conveniently various types of energy. Lithium-ion batteries are an excellent example of an Energy Storage System.
- EVSE (Electric Vehicle Supply Equipment): is to supply electric energy to recharge electric vehicles and charge for the operation of electric cars or plug-in hybrid electric-fuel vehicles.
- FC (Fuel Cell): an electrochemical cell that converts the chemical energy of a fuel (hydrogen) and an oxidizing agent into electricity via a pair of redox reactions.
- FFC (Flat Flexible Circuit): these circuits can fold into nearly any shape due to their smaller size and flexibility. They are durable and capable of handling high density.
- IGBT (Insulated-gate bipolar transistor): a three-terminal power semiconductor device primarily used as an electronic switch that combines high efficiency and fast switching.
- ICE (Internal Combustion Engine): a heat engine in which fuel combustion occurs with an oxidizer in a combustion chamber, an integral part of the working fluid flow circuit.
- NTC (Negative Temperature Coefficient) Thermistor: these are resistors with a negative temperature coefficient. It means that the resistance decreases with increasing temperature. NTCs are primarily used as resistive temperature sensors and current-limiting devices.
- SOC (State of Charge): the level of charge of an electric battery relative to its capacity. The units of SoC are percentage points.
- Thermal Efficiency: defined for engines and devices that convert energy into heat to work. It is a dimensionless performance measure of a device that uses thermal energy.
- UC (Ultra Capacitor): a high-capacity capacitor with capacitance value much higher than other capacitors, but with lower voltage limits, that links the gap between electrolytic capacitors and rechargeable batteries.
*Trademark. Amphenol is a trademark of Amphenol Corp. Other logos, product and/or company names may be trademarks of their respective owners.
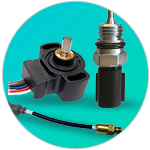
Test Your Knowledge
Sensors VI
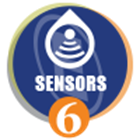
Are you ready to demonstrate your Automotive Sensors knowledge? Then take a quick 15-question multiple choice quiz to see how much you've learned.
To earn the Sensors VI Badge, read through the learning module, attain 100% on the Quiz, and leave us some feedback in the comments section.
Top Comments