The use of variable frequency drives (VFD) can increase efficiency in motors. Modern VFD algorithms monitor a motor’s load, making adjustments when required.
Electric motors and drives work in conjunction to convert electrical energy to mechanical energy. Most types of machinery that feature moving parts make use of electric motors; these include vehicles, appliances, fluid pumps, and industrial robots. For more background on motors and the fundamentals of how motors and drives work, take a look at element14's Essentials on Motor Control and Variable Frequency AC Drives.
Related Components | Related Tech Spotlight | Take the Quiz
Reducing power consumption while improving efficiency is a major goal of most electronic system designs. This is especially important with the proliferation of battery-operated devices, as well as being able to optimize the use of renewable energy. This learning module discusses methods of improving motor and drive efficiency with the use of variable frequency drives (VFD).
2. Objectives
Upon completion of this module, you will be able to:
- Describe what a variable frequency drive (VFD) is
- Understand how VFDs can improve efficiency
- Explain modern control algorithms, and how they work to optimize energy usage
- Discuss various sources of instability and inefficiency in AC drives
3. Basic Concepts
Before discussing drive efficiency, let’s quickly review how AC motors work. A typical AC induction motor connects directly to the utility power supply, which runs the motor at its synchronous, or rated, speed. The speed is dependent on the frequency of the current being supplied to it and the number of poles the motor has. The synchronous speed can be calculated with: N = 120 * f/P
Where f is the frequency and P is the number of poles. For a 4-pole motor running on 60 Hz AC power, the synchronous speed is: 120 * 60 / 4 = 1800rpm
A variable frequency drive (VFD), otherwise known as an adjustable frequency (AF) drive, is a device that controls the speed, direction, torque, and horsepower of an AC motor. Torque and horsepower are directly related and can be expressed in the equation: HP = (T * N) / 5252
Where HP is the horsepower provided by the motor, T is the torque of the motor in foot-pounds, and N is the synchronous speed of the motor.
The task of a VFD is to convert the utility power to an adjustable frequency and voltage, allowing for control of a motor's speed. To change the frequency, the incoming 60 Hz (or 50 Hz) AC power must be converted to DC. The DC signal is then converted back into AC at a different frequency using an inverter. Inverters typically generate AC power by switching the current on and off very quickly; by speeding up or slowing down this switching, an AC signal can be created at any frequency. The three most common inverter types in use today are pulse width modulation (PWM), current source inverter (CSI), and variable voltage inverter (VVI). Modern VFDs typically use PWM inverters.
One factor which affects the efficiency of motors are harmonics, frequencies at which unwanted and unusable voltages and currents are introduced into the system. Harmonics can affect the total power factor, which is the ratio of the power in to the power out, including any losses due to harmonics. The ideal power factor is 1.00, or unity, which signals no power loss and maximum efficiency for the motor.
Increasing efficiency with VFDs

Figure 1: Mechanical throttling device vs. VFD
In the early 1970's, the energy crisis forced engineers to come up with ways to reduce power consumption; the use of VFDs grew quickly due to their efficiency and comparatively reduced maintenance needs. In the example of a pumping application, one of the traditional methods of controlling the fluid flow was mechanical throttling. The system would pump at its full synchronous speed, and flow was limited using a valve. A VFD, on the other hand, can control the flow by altering the speed of the AC motor driving the pump. This can reduce power consumption and increase efficiency. Figure 1 illustrates the pumping system using mechanical throttling vs. a VFD.

Figure 2: Energy saved using a VFD vs. a Valve
Figure 2 shows the energy savings when using a VFD. The green area represents the energy saved.
Technology has evolved and improved over the years, and modern VFDs employ algorithms that make them more efficient than ever before. Modern control algorithms can dynamically adjust the motor’s operating point based on load conditions, reducing power consumption, and improving energy efficiency.
Analysis
The most significant factors that determine the operating point of a VFD-driven motor are voltage and frequency output from the drive, along with the motor load. Many industrial applications have constant load requirements. In these cases, the volts per hertz (V/Hz) ratio is kept constant, producing a constant torque for the load. In a graph, a constant V/Hz ratio is represented as a straight line connecting two points, (0 Hz, 0 V) and (frated, Vrated), where frated is the rated frequency (typically 50 or 60 Hz) and Vrated is the rated voltage. In these cases, the voltage required for a desired reference frequency (fref) is equal to fref * Vrated / frated. This is known as linear control.
For some applications, the torque needed to drive the motor load varies based on the shaft speed of the motor, which is set by the frequency of the VFD output. Variable torque (VT) applications include hydraulics and HVACR, which use induction motors to drive pumps and fans. The pump or fan requires less torque to power it at a lower reference frequency than for a higher one. In these cases, a linear V/Hz curve may provide a higher than necessary voltage, especially in the region where fref is lower than frated. For these applications, many VFDs provide a squared (quadratic) V/Hz control method.
Figure 3 illustrates the load characteristics for both a constant torque (CT) and a variable torque (VT) load, in addition to the frequency curves (V/Hz) for both linear control and quadratic (squared) control.


Figure 3: Constant torque vs. variable torque (left) and linear V/Hz vs. quadratic V/Hz (right).
Reducing the input voltage to an induction motor increases efficiency by reducing motor core losses. Input voltages that are too high can cause motor core losses in the form of heat and noise.
The linear and quadratic/square curves depicted here are known as static control methods, meaning that the voltage output is dependent only on fref, and do not consider the actual motor load. When the motor load is low, the voltage generated by either method may be excessive, causing unnecessary core losses. If the motor load is high, the voltage generated from the quadratic control method may be insufficient, potentially causing the motor to overheat or stall.
A modern control algorithm considers all aspects of the system. The operating parameters of the motor are monitored in real-time, and the output voltage of the VFD is adjusted accordingly to find an operating point that maximizes efficiency and motor stability.
Eaton’s Active Energy Control Algorithm
Eaton Corporation has created its Active Energy Control algorithm with the goal of optimizing energy use, while maintaining motor stability. The algorithm follows these basic steps:
- The drive output voltage is initially set at the voltage determined by the linear V/Hz method for the same fref. This ensures motor stability.
- Voltage is reduced incrementally in an effort to optimize energy usage. At each increment, several real-time parameters of the motor are monitored for signs of instability.
- At the optimal zone of operation (lowest energy usage, while maintaining stability), the drive output voltage is kept constant until a command to the drive triggers a change. Potential changes include a change in fref, or changes in the motor’s real-time parameters.
After the output voltage is stable, the drive continuously monitors the motor, looking for signs of instability. One potential cause of instability is excessive reduction in the supplied voltage, which causes the motor current to rise. Excessive current can not only lead to motor instability, but other conditions, such as motor copper loss. The algorithm keeps an eye on motor slip and motor current, and intervenes to make sure the voltage level is not too low.
Changes in the motor load can also lead to instability. The algorithm is able to adapt to slower changes by adjusting the voltage level when gradual increases in motor slip and motor current are detected. Abrupt changes are more challenging; the algorithm must respond to a rapid increase in motor slip or motor current with an equally fast increase in output voltage.
Testing the algorithm
Eaton’s algorithm was tested with abruptly changing reference frequencies and motor loads with the goal of understanding its stability as well as its efficiency. The algorithm’s performance was compared to other V/Hz control methods.
- Stability Tests
Stable performance is a minimum requirement for a VFD algorithm; without stable performance under changing conditions, the algorithm is not viable. To compensate for abrupt changes in reference frequencies or motor load, the algorithm must change the output voltage as quickly as possible. If the change is too slow, the motor may become unstable. Eaton’s algorithm was tested for incremental frequency changes, ranging from ±1 Hz to ±15 Hz, in addition to abrupt changes in motor load. The algorithm was able to keep up, successfully adjusting output voltage to prevent instability conditions, including overcurrent trip, motor stall, or overload.
- Energy Savings Tests
Eaton conducted two sets of tests, one in a lab environment and one at a waste water treatment plant. In the lab tests, a 50hp motor was tested, driving a generator that was powering resistor banks set up to emulate a real load from a fan or pump. Figure 4 shows the results of the lab tests. When compared to existing static and dynamic V/Hz control algorithms, Eaton’s Active Energy Control algorithm showed higher percentages of energy savings.

Figure 4: Energy savings of the Active Energy Control algorithm
In the real world testing at a waste water treatment plant, the Active Energy Control algorithm controlled a VFD that was driving a centrifugal pump. For this particular installation, the motor and VFD are both rated at 50 Hz. The energy savings over linear V/Hz mode at various frequencies are illustrated in Figure 5.

Figure 5: Energy Savings of the Active Energy Control algorithm vs. Linear V/Hz mode
A final test was performed by a third party test provider. In this test, the VFD is used to drive a 20hp motor, which in turn, drives a 24 ½ inch blower. Input power was measured for a variety of frequencies between 30 Hz and 55 Hz. Figure 6 illustrates the energy savings over linear V/Hz mode, as well as a flux optimization method and a dynamic V/Hz control method from different vendors.
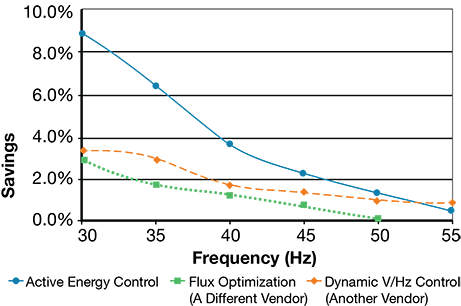
Figure 6: Energy Savings for various V/Hz algorithms compared with linear mode
- Harmonics and Bearing Currents
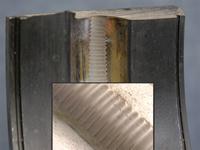
Figure 7: Fluting
As discussed earlier, harmonic voltages and currents lower system efficiency. Harmonics, along with magnetic imbalances, can induce voltages on the shaft. When shaft voltages are high enough (typically greater than 50V) to overcome the breakdown voltage of the bearing lubricant, bearing currents can occur. Bearing currents are currents that flow through the bearing and through the motor or motor frame, resulting in fluting in the bearing race, as illustrated in Figure 7. In a motor with fluting, bearing rotation is no longer smooth.
Bearing currents can be prevented with a combination of techniques.
- Using shielded motor cables with symmetrical protective earth wires provides a low impedance path for currents caused by the high frequency common mode voltages to return to the drive.
- Using specially insulated bearings on the opposite drive end or insulated load coupling can stop the flow of current.
- Shaft grounded brushes dissipate voltage buildup along the shaft.
- Finely stranded grounding cables can more effectively ground high frequency currents.
- Filtering can be applied to remove high frequency currents; however, because is no universal filter for bearing currents, filtering is often custom designed and very expensive.
4. Glossary
- Bearing race: the outer and inner race of a bearing are in combination the surrounding housing for the balls in the bearing.
- Bearing current: unwanted currents caused by an induced voltage on the shaft that flow through the bearing and through the motor or motor frame.
- Fluting: damage that occurs when AC or DC current actually passes through the metal bearing. The damage has a washboard-like appearance. The most common indicator for fluting is an audible noise emanating from the bearings.
- Harmonics: frequencies at which unwanted and unusable voltages and currents are introduced into the system.
- Horsepower: the unit of measurement for the amount of work a motor can output. All motors are rated according to their horsepower.
- Inverter: a device that converts DC (direct current) power to AC (alternating current) power.
- Motor drive: an electronic device that controls the power that is sent to a motor.
- Torque: a measurement of rotational force.
- Pole: a north or south magnetic field of force generated via permanent magnet or a current passing through a coil of wire.
- Power factor: the ratio of the power in to the power out of a device. A power factor of 1.00 (called “unity”) is ideal.
- Reference frequency (fref): the signal that the VFD sends to the motor that controls its speed.
- Variable Frequency Drive (VFD): a type of controller that drives an electric motor. VFDs are capable of controlling the speed of the motor by varying the frequency and voltage supplied to it.
*Trademark. Eaton is a trademark of Eaton Corp. Other logos, product and/or company names may be trademarks of their respective owners.
Test Your Knowledge
Motor Control II
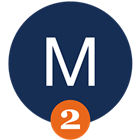
Complete our Essentials: Motor Control II course, take the quiz, and leave your feedback to earn this badge.
Are you ready to demonstrate your motor control knowledge? Then take this 10-question quiz. To earn the Motor Control II Badge, read through the module, attain 100% in the quiz, and leave us some feedback in the comments section.
Top Comments