In the world of warehouse automation, hardware stands as a crucial driving force behind the upcoming wave of technological advancements. New technologies are constantly emerging, making automation more accessible and efficient, even for smaller operations. A notable breakthrough has been the adoption of lithium-ion battery technology, which has significantly improved the performance of electric vehicles and robots, making them smaller, yet more powerful. There are several other important but lesser-known innovations advancing warehouse automation; these hardware innovations play an important role in making automation run smoothly.
Optimizing Battery Performance with Battery Management Systems
Recent advancements in lithium-ion battery technology have enabled significant improvements in energy storage capacity within a smaller form factor, often referred to as "energy density." Reducing the battery size while increasing energy storage has been a primary focus for battery and fuel cell manufacturers. Equally important is the drive to enhance energy efficiency in both storage and utilization. The central component addressing these goals is the battery management system (BMS).
Figure 1: Components of BMS (Source: All About Circuits)
The BMS can be considered the brain of the battery; it plays a critical role in determining how the battery supplies power, manages recharging, and efficiently distributes power from the battery cells. Typically integrated within the battery pack of electric forklifts, automated mobile robots, or autonomous guided vehicles, the BMS constantly monitors battery health, power levels, and charging status. It can also be paired with telematics to keep track of temperature and workloads.
In the current landscape, manufacturers differentiate themselves based on two primary factors. First, they focus on how rapidly their batteries can recharge. Second, they emphasize the intelligence of their BMS to enable smarter and more efficient energy usage. A smart BMS necessitates intelligent connectors for power, signal, and data. Connectors act as conduits, facilitating seamless communication between devices.
What is Opportunistic Charging?
In the near future, the concept of a dedicated warehouse charging room will become a thing of the past. As lithium-ion batteries replace the traditional lead-acid models, warehouses will no longer need to allocate space for forklifts and idle batteries to recharge for extended periods. Instead, the trend of opportunistic charging will become the new norm, allowing forklifts, mobile robots, or automated guided vehicles (AGVs), to plug into nearby charging stations and achieve a full charge within 15 to 30 minutes. However, this trend brings new challenges for connectors and cables that were originally designed for traditional charging methods.
Figure 2: Battery Charging in Warehouse Automation
Opportunistic charging allows for multiple mating cycles per day, far more than the traditional charging methods. Traditional connectors were designed for once-a-day charging over an extended period. With opportunistic charging, equipment is charged several times a day. Additionally, to support quick charging, connectors and cables must also transmit more current. A third requirement is confirming secure connections in a fully automated system. Because there is no human guidance, the entire process relies on sensors, motors, drives, and connectors.
To tackle the challenges posed by this dynamic environment, engineers build tolerances into the vehicle's system. These tolerances allow for a secure charging connection to be established, even in situations where the alignment isn't perfect due to the uneven warehouse floors or unexpected obstacles.
Increasing Interoperability and Cross-Compatibility
Dynamic Series
Shop our wide variety of Dynamic Series Connectors from TE Connectivity.
Don't forget to join our discussion.
Interoperability has become a significant trend in warehouse automation, reflecting the growing demand for platform-agnostic charging connectors, cables, and stations. However, at present, this seamless compatibility remains elusive. Each brand of forklift, autonomous mobile robot (AMR), and AGV has its own proprietary charging connector, lacking cross-compatibility. While this might not pose a problem for smaller operations that use a single brand of equipment, it becomes a real issue for large warehouses with diverse fleets consisting of multiple brands.
To address this challenge, TE Connectivity (TE) is collaborating with other companies and trade groups to advocate for industry standards that promote cross-compatibility between brands. The goal is to enable companies to use a single charging connector and make it easier for the end users to have a unified charging station that can charge the entire fleet, regardless of the equipment's brand.
Interoperability goes beyond mere user convenience. It has the potential to allow AMRs from different brands to share status information, operational conventions, and other crucial details, making warehouse automation more efficient and unlocking new avenues for innovation. By establishing interoperability standards, the industry aims to create a more unified and streamlined approach to charging, ultimately benefiting large warehouse operations and driving further advancements in warehouse automation.
The Evolution of Wireless Charging
A promising trend in warehouse automation is the exploration of wireless charging options for electric forklifts. This technology offers several potential benefits, such as resolving safety concerns, reducing maintenance costs, and allowing for unlimited mating cycles. However, the road to making wireless charging a reality comes with some challenges that need to be addressed.
One significant challenge is the limited power offered by most current wireless charging systems, ranging from 1kW to 3kW. While sufficient for smaller vehicles, it falls short for larger forklifts that typically require 10kW to 25kW for charging. Another obstacle is the need for a substantial surface area on the vehicle to accommodate the wireless charging system. For instance, a 3kW system demands around 25cm x 25cm of space on a forklift. While this is not an issue for larger forklifts, it presents challenges for smaller AMRs.
Despite these challenges, the benefits of wireless charging are significant and worth exploring. It can lead to reduced maintenance requirements, virtually unlimited mating cycles, and the freedom to dock from any direction. Some technologies even enable dynamic charging, allowing vehicles to charge while in motion. Additionally, wireless charging eliminates the need for exposed contacts, making it particularly valuable in cold chain or outdoor applications. The possibility of a flush design is also advantageous in areas where food is handled or in clean rooms.
Dynamic Series Connectors
The Dynamic Series connectors from TE Connectivity offer an efficient and reliable solution for enabling the transfer of data and power within charging systems and battery management systems. The Dynamic Series is available in a variety of form factors that can meet most applications, as well as having standardized contacts to reduce the amount of application tooling required (standard crimp and spring clamp variations are available).
How Will Manual and Autonomous Charging Complement Each Other?
In the automated warehouse of the future, both manual charging and autonomous charging options will coexist. Rather than one technology replacing the other, they will serve as essential redundancies, ensuring continuous operation.
Manual charging is here to stay and will remain as a reliable fail-safe option when automated charging is not feasible. Market leaders in the industry emphasize the importance of redundancy. Depending solely on a single type of charging can lead to complications. For instance, if all self-docking charging stations are occupied or if one malfunctions, an alternative charging solution becomes crucial. The ability to switch between manual and autonomous charging provides this much-needed redundancy, ensuring warehouses can continue their operations efficiently.
Ultimately, both options will be integral to the functioning of automated warehouses, offering flexibility and resilience in various situations. As the industry continues to evolve, engineers and companies recognize that providing a choice between manual and autonomous charging is vital to meet the diverse needs of warehouses and ensure smooth, uninterrupted operations.
Looking Forward: What are the Trends in Warehouse Automation?
In partnership with
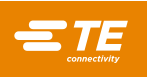
Warehouse automation is undergoing rapid advancements, driven by innovative hardware trends, enabling warehouses to embrace automation more effectively, improve energy efficiency, and optimize overall workflow. The increasing demand for efficiency and scalability in warehouse operations has led to significant developments in charging technology, battery management systems, and autonomous robots. TE Connectivity plays a significant role in modernizing warehouse automation, not only by developing connectors that stand up to the rigors of industrial environments, but also working with other companies to develop new standards for maximizing interoperability between manufacturers.
As warehouses become increasingly automated, what will be the effects on the products that they produce?
Please tell us in the Comments section below.