An overview of cooling techniques for electronics, with a focus on electronically commutated (EC) fans.
Using less power to cool electronics
Every electronic device generates heat when operating. This unwanted heat must be removed because an increase in temperature will often degrade the performance and lifespan of the device. Active cooling is one way to keep a device's temperature within permissible operating limits. In active cooling, a system fan is utilized to produce airflow around the heat-generating components, effectively removing heat from the equipment. However, a fan can generate noise and consumes additional power – a significant factor in battery-powered IoT devices. This article explores the various methods of cooling electronics and introduces the concept of electrically commutated (EC) fan technology.
Methods of cooling electronic equipment
Electronic equipment can be cooled with several techniques. These methods include:
- Natural convection cooling uses motion caused by density differences in a fluid due to a temperature difference. A fluid expands and becomes less dense when heated. The lighter fluid rises, causing a motion in the fluid called natural convection currents. Natural convection currents can be used to circulate the air in a control enclosure and keep it cool.
- Forced air convection cooling uses fans to blow air through the enclosure that houses the electronic components, boosting natural convection. A typical forced convection system includes a fan with a filter to increase the velocity and flow rate of the fluid, in addition to increasing the amount of heat transfer.
- Heat exchangers transfer heat from electronic enclosures into a fluid. The heat from this fluid is transferred to a second fluid inside the heat exchanger. The original fluid (liquid or gas) is cooled and returned to the assigned location, restarting the Fans or pumps are used to keep the fluids in motion.
- Air Conditioners use refrigerant and air-moving systems to cool air. A typical air conditioner transfers heat from the enclosed components by circulating air around and through them. This air is then cooled, dehumidified, and returned to the enclosure. The cooling takes place within the air conditioner and the heat is discharged using a vapor compression refrigeration cycle.
- Thermoelectric Coolers, or Peltier coolers, have fans inside and outside the enclosure and use a thermoelectric unit in place of typical fluid-based refrigeration systems. Thermoelectric units are essentially an array of semiconductors placed between two ceramic plates. When a direct current is applied to the semiconductor array, heat is driven from one plate to another, creating a cold and warm side.
- Vortex Cooler: Vortex coolers create a stream of extremely cold air from a continuous supply of filtered compressed air. The cold air is first injected into the enclosure, displacing the warm air, which is pushed through the vortex cooler. Vortex coolers can also be used where the ambient temperature exceeds the enclosure temperature.
Figure 1: Vortex Cooler (Source: Xue, Yunpeng, Univ. of Adelaide)
What are EC fans?
Electronically commutated (EC) fans have motors that operate on an alternating current (AC). These motors closely resemble direct current (DC) motors. An EC motor is 'electronically commutated,'; it utilizes built-in electronic circuitry to control the speed and direction of the motor’s rotation. resulting in greater energy efficiency and quieter operation compared to a traditional DC fan that relies on mechanical brushes for commutation. EC motors and fans can be connected directly to the AC mains supply, rather than a separate DC power supply. This feature makes them easy to retrofit and provides greater control and higher efficiency.,
The Basics of DC and AC Motors
All electric motors transform electrical energy into mechanical energy, but they do this in different ways. The technology used to transform the energy is determined by the power supplied to the motor, which, in turn, influences how magnetic fields are formed and regulated.
AC Induction Motor: An AC Induction motor is suitable for all types of machines. This simple and robust motor generally runs at a constant speed, which changes slightly when mechanical loads are applied to the motor shaft. AC motors are engineered to function optimally at a specific speed range due to the fixed line frequency they operate on. This allows them to achieve peak efficiency at a designated point on their performance curve. However, their efficiency noticeably declines when they operate outside this range. Engineers can use a variable frequency drive (VFD) to increase or decrease the frequency of the AC supply, but they tend to be bulky and expensive.
DC Motor: DC motors run on DC power and produce mechanical torque. DC motors have high starting torques and can easily absorb sudden increases in load. They are widely used in adjustable-speed drives and position control applications. DC motors are preferred where wide speed range control is required as they are simpler and less expensive than AC motors. Speeds lower than the base speed can be controlled by armature-voltage control, while higher speeds are achieved by field-flux control.
How does an AC/EC fan work?
EC motors house electronics that convert AC power to DC These electronics also perform the commutation and control the speed by regulating the power to the motor. The onboard electronics, through each winding, provide the appropriate amount of current in the correct direction and at the precise time. This action generates magnetic poles within the stator, which interact with the rotor's permanent magnets. The position of each magnet is determined using Hall effect sensors. A combination of attraction and repulsion forces is achieved by attracting the appropriate magnets in sequence to the magnetic poles in the stator while simultaneously charging the remaining stator windings with reverse polarity. These attraction and repulsion forces combine to achieve rotation and produce optimal torque.
Figure 2: The Schematic Structure of EC Motors (Source: rses.org)
Why are AC/EC fans more energy efficient than AC fans?
EC fans offer the same air volume output as AC fans but use less electrical power, consuming 70% less energy than standard AC technology. The design of standard AC fans enables them to operate at a predetermined point on their performance curve, which coincides with their peak efficiency. The efficiency can drop off considerably on either side of this operating point. On the other hand, EC fans have an almost flat efficiency curve, which varies relatively little across the speed range. This allows the EC fan to adjust to the level of cooling needed, thereby cutting energy waste from fans running faster than necessary.
AC/EC Fans from Sanyo Denki
EAO has introduced the new Sanyo Denki San Ace 172AD 9AD Type ACDC and San Ace 172AD 9ADW Type Splash Proof ACDC fans. These centrifugal fans provide a maximum static pressure of 195 Pa and maximum airflow of 6.7 m3/min or 236 CFM. The 9ADW splashproof versions are additionally sealed (IP56) to cope with moisture-laden environments. These fans have two voltage options of 115V/60Hz and 230V/50Hz input. Both types utilize EC motor technology that offers significant power savings over traditional AC fans – typically reducing running costs by over 30%.
San Ace 120AD AC/EC Axial Fan
Energy efficiency can be increased further if the PWM control input is used to reduce fan speed. The power consumption drops to 48% at 60 Hz and 58% at 50 Hz respectively when the speeds are reduced with PWM control. The fans have an expected life of 40,000 hours at 60°C (survival rate of 90% if run continuously at the rated voltage in free air and normal humidity). They are well-suited for blowing applications in air conditioning systems, cooling inverters, and the housings of communication systems with high mounting density.
San Ace 190AD AC/EC Centrifugal Fan
Summing up: Energy efficiency when cooling electronics
In partnership with
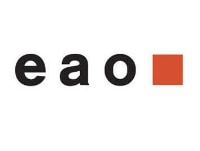
An adequately set up cooling unit facilitates superior active cooling of an electrical enclosure. Cooling units protect electrical devices from exposure to temperatures beyond their acceptable operating limits. EC fans attain an efficiency level of up to 90%, which translates to better primary energy utilization, reduced heat loss, and longer service life. Depending on the application, EC fans can offer shorter payback than permanent split capacitor (PSC) motor-based fans. EC fan technologies developed by Sanyo Denki are reliable and efficient. With their reduced power consumption, Sanyo Denki EC fans can lower operating costs as well as extend battery life for portable and IoT devices.
What kind of applications and improvements do you see possible with more powerful and efficient cooling?
Please tell us in the Comments section below.