Connectors Essentials Series - Part 6
Evolution is natural to a vibrant automotive market, and experts anticipate that by 2030 all vehicles on the road will be networked. Connected and automated vehicles need high bandwidth and fast signal processing to support an agile control system that distributes data to in-vehicle processing units. Connections to the automobile's electronic data networks must be of superior performance and reliability. Emerging solutions and technologies create an effortless driver connectivity experience and improve road safety. This learning module discusses the application trends shaping next-generation automated driving vehicle technology, such as ADAS/AD, ECU, Radar, LiDAR, digital cockpit/in-vehicle infotainment, and cameras. It focuses on various types of automotive connectors distinctively designed for in-vehicle systems.
Related Components | Test Your Knowledge
sponsored by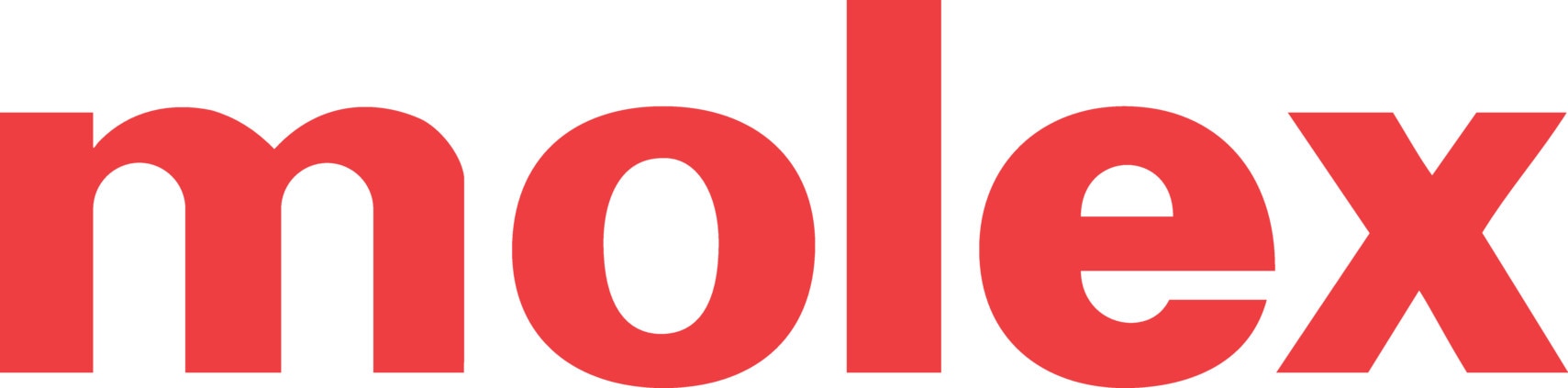
2. Objectives
Upon completion of this module, you will be able to:
- Explain how current trends are changing vehicle technology and automotive design
- Describe the different types of automotive connectors
- Understand connector design requirements for in-vehicle electronic systems
- Discuss automotive connectors for in-vehicle electronic systems such as ADAS, ECU, Radar, LiDAR, and others
3. Scope
The accelerated development and prototyping of autonomous and semi-autonomous vehicles has created a demand for high-speed, ultra-reliable, and secure end-to-end network integration. It follows that extensive cabling for an increased number of new connections will have to compete for space in condensed automotive architectures. Reliable high-speed data is essential for the rapid increase of electronic control units (ECUs), interior and exterior sensors, advanced telematics, and infotainment systems. We will discuss the different types of connectors used in automotive applications for in-vehicle electronic systems such as automated driving, high-performance terminal connection systems, in-vehicle infotainment, and the progressive need for space-saving in vehicles.
4. Basic Concepts
The sheer volume of electronics, software, and computing power in today's vehicles has revolutionized both how they function and our relationship with them. Wired vehicle communications link all sensors and data processing ECUs that discern software algorithms and external data to unify the vehicle's operating environment. Quick signal processing and high bandwidth are vital to the automated car. As such, vehicles require an agile control system that distributes the data to the processing units deployed within the vehicle. Today's automotive designs require better in-vehicle connectivity, thereby utilizing connectors that offer reliable high-speed, high-power signals and high-bandwidth to every sensor and system within the vehicle. In this section, we will review these systems to better understand in-vehicle connectors' needs and applications.
- 4.1 In-Vehicle Electronic Systems Overview
Automated driving: ADAS/AD ECU, Radar, LiDAR, Cameras
Autonomous/adaptive driving plays a significant role in minimizing accidents. Advanced driver-assistance systems (ADAS) like automatic braking, adaptive cruise control, lane-keeping, and other active safety systems are now a standard safety feature in modern vehicles. They are a critical underlying technology when it comes to emerging autonomous vehicles. The increasing volume of electronic control units and their subsequent integration with various sensors now lends adequate computing capabilities in cars to reinforce ADAS deployments. Different kinds of sensors, like cameras, radio detection and ranging (radar), and light detection and ranging (LiDAR), enable several diverse ADAS solutions. Vision-based ADAS, which primarily utilizes cameras as vision sensors, is prevalent in most modern vehicles.
Figure 1 illustrates a vehicle architecture with a combination of sensors, including cameras, radar, LiDAR, and ultrasonic. Cameras are located where they can discover objects outside of the vehicle. Vision-based ADAS utilizes one or multiple cameras to capture images. This embedded system detects, analyzes, and then tracks various items. In a high-end ADAS, cameras monitor both inside and outside the vehicle.
LiDAR functions by hitting an object with a laser beam, and then the time elapsed for the light to rebound to the sensor is measured to compute the object distance. Such systems can accomplish high-resolution 3-D images and work at longer ranges compared to camera systems. Radar systems radiate microwaves, and an object's distance and speed can be estimated by the frequency variation of that reflected wave according to the Doppler effect. They can discover items at longer distances and travel farther in contrast to optical light.
These sensors generate massive quantities of data, requiring immense computing power, speed, and bandwidth to synthesize in real-time and lead to safe decisions in just a few milliseconds. Semiconductor companies have developed new controllers that allow high bandwidth data transmission up to 10 Gbps or more. They require reliable, superfast, and universal standard end-to-end multi-zone vehicle network architectures. The vehicles will transform from mobile computers to data centers on wheels, that is, autonomous vehicles that make complex decisions in real-time.
The use and quantity of electronic control units (ECUs) in automobiles has increased from merely a few to a hundred or more in premium vehicles. They control everything from fuel injection, ignition timing, and engine management to traction control and anti-lock braking. These systems have recently extended to adaptive cruise control lanes or safe distance-keeping (SAE levels 1 and 2 -partial automation and driver assistance) and automated braking.
Digital Cockpit/In-Vehicle Infotainment: Head-up Display, Central Info Display
There is a demand for simpler, more user-friendly information management inside the vehicle. Safety, user experience, and connectivity are driving future digital cockpit developments.
The digital cockpit integrates cluster, infotainment, and Head-up Display screens. It is, however, insufficient to simply have a few displays in the vehicle. The displays must be connected to form one unique canvas. Modern Systems-on-Chips (SoC) with powerful processing capabilities enable multiple subsystems to be run simultaneously. Such performance levels provide the opportunity to blend different algorithms and a digital cockpit to enable autonomous driving on a single chip.
Automobile manufacturers pack multiple entertainment and convenience features into their cars. These are referred to as In-Vehicle Infotainment (IVI) systems. The IVI system is essentially an integrated system that supports automobile navigation, instrument panel, radio, multimedia connection with DMB (Digital Multimedia Broadcasting), external devices, and various sensors. IVI devices offer entertainment services like movies, games, TV, SNS, and navigation.
A windshield Head-up display (HUD) displays information to the driver at the driver's eye level. This permits the driver to look towards the road while acquiring speed and other pertinent information. As displayed in the following figure, the HUD display can be projected on a windshield section or a transparent surface in-between the windshield and the driver. Drivers acquire vital information like speed and warning signals without consulting the instrument cluster or secondary display.
- 4.2 Review of Connector Design Basics
A connector is a device that connects two or more circuit points, signals, or subsystems with electrical integrity, mechanical durability, environmental protection, and safety. Connectors offer a safe, convenient, and quick process for linking and detaching components, sub-assemblies, prototyping, operation, manufacturing, or installation. Connectors should be tough to endure mechanical forces associated with the application. They should resist the corrosion that may occur and worsen the connection over time.
Connectors come in many styles and types, but all share a few common attributes. Any connector has three principal parts: housing, contacts, and shell. The housing component of a connector electrically insulates the contact terminals and provides them mechanical durability and environmental protection. The shell encapsulates the connector housing, giving the latter extra protection and strength. Zinc alloy, nickel-plated shells offer corrosion resistance, for example. The contact is made from low resistance but highly conductive material that allows electrical current to flow easily through the mated contacts.
Typical contact metals include brass, high copper alloy, and phosphor bronze. Contacts are frequently plated for extra strength, corrosion resistance, and better conductivity. Gold, silver nickel, palladium-nickel, and tin are used as plating materials. Connector housings offer the needed insulation between the connector contacts, termed the Dielectric Withstand Voltage rating. An important function of the connector housing is to stop contact interface contamination. Such contamination is staved off by the incorporation of sealing devices inside the housing.
Mechanical integrity holds the key to a secure connection. The mechanical connection should suit the conductor's current transporting capacity and offer easy installation, resulting in a reliable and safe electrical connection. Corrosion is of two main types: galvanic and oxidation. Both affect the long-term performance and initial contact of an electrical connection.
A few design considerations should be observed during connector selection. These include the type of contacts and their numbers (whether sockets or pins and their respective specifications), regulatory and environmental ratings (RoHS, REACH, ISO 10993, UL), cable configuration, cable diameter, materials, shape, shielding requirements, strain relief requirements for both cable and connectors, current and voltage needs, rating or Ingress Protection (IP) requirements, a locking mechanism (if present), cleaning, sterilization, and disinfection requirements.
A connector must adhere to electrical and mechanical international standards like the IEC 1076-4-1 01 specifications. A better connector design implies better electromagnetic signal propagation conditions. Another key application objective is to complement the connector to that printed circuit board. The connector must also match vias and other printed circuit board attributes. An optimum match is attainable only through a prudent selection of signal/ground ratio, connector pin assignment, and geometry.
Current and voltage levels are perhaps the two most necessary factors to observe during connector design. Current flow across the contacts of the connector results in heat generation, and consequent temperature rise of the local environment. Signal contacts are utilized in low voltage applications, and power contacts manage high voltage applications. Contact material selection is contingent on a blend of concurrent factors such as cost, mechanical requirements, size limitations, and electrical requirements.
- 4.3 Connector Design Considerations for In-Vehicle Electronic Systems
Automotive technology advancements have enabled smarter, more feature-rich in-vehicle applications and, consequently, refined vehicle performance. Such a transformation has pushed data requirements, creating a need for connectivity that can manage increased high-speed data. Automobile systems must manage both signals and power without harmonic distortion and with high reliability.
To extract the necessary superior performance for next-gen automotive features, engineers must consider a variety of challenges - constrained space, increased harness weight, hazardous environments, limited network bandwidth, and complex networks, among others. Automotive components must function across extreme temperature variations, from freezing temperatures to extreme heat. The vehicles must also simultaneously withstand vibrations and mechanical shocks, frequent thermal cycling, constant moisture exposure, electrical, electromagnetic, and electrostatic interference, humidity and solvents, and even possible mechanical stresses (the result of flexing PCBs).
Communications architectures inside the vehicle are designed for higher speeds. Flawless data communication is a must. Connections should be reliable and robust, and data links must satisfy stringent electromag¬netic compatibility (EMC) needs. They must not unintentionally radiate unwanted emissions and must be invulnerable to accidental electromagnetic fields. The in-vehicle communication channels will be exposed to extreme vibration and temperature. Connections should be compact, to fit communications architecture. ADAD/AD and In-Vehicle Networks (IVNs) have radically changed cabling requirements, as an increasing number of vehicles need greater signal transmission and higher connectivity. Secure and reliable high-speed networking cables for in-vehicle networks are critical.
5. Analysis
The automobile of the future melds advancements in AI, electrification, connectivity, and computing power. New vehicle electronics need increased speed, signal integrity, and modularization to transfer higher bit rate data streams, with a considerable increase of various engine compartment systems, cameras HMI, and radars that need multiple flexes and PCB assemblies. Such assemblies need connectors with better signal integrity for speed and robustness in demanding environments.
- 5.1 Trends
A few trends that are influencing the development of new automotive connectors are:
- Human Machine Interface (HMI) Demands Connections: An increasing number of applications use interfaces to communicate. The majority of user interfaces come with flex-to-board (F-to-B) connection points that need a flexible printed circuit board (PCB) or a board-to-board (B-to-B) connector. The demand for sensors, cameras, microphones, and speakers is driving greater modularity, which demands more (and higher quality) flexible printed circuits (FPCs), flexible flat cables (FFCs), and B-to-B and wire-to-board (W-to-B) signal connections.
- Harsh Environments Mandate Durability: PCBs and Flex assemblies are becoming increasingly complex. Harsh environments require high retention force features and better signal integrity performance to withstand shock and vibration, pushing the need for improved FPC, FFC, B-to-B, and W-to-B signal connections.
- Space-Constrained Profiles Require Flexibility: The volume of transportation applications is becoming increasingly space-constrained. Multiple profiles and micro-connector orientation options offer designers much-needed flexibility to solve space, connector entry points, and location challenges.
- 5.2 Connectors for In-Vehicle Electronic Systems
The increase in electronic systems such as powertrain electrification and sophisticated advanced driver assist systems is changing vehicle technology and automotive design. As a result, extensive cabling creates many new connections competing for space in high-density automotive architectures. Miniaturized systems based on high-performance terminal connection systems satisfy requirements for reduced package size, wire gauge, space optimization, and weight. In this section, we will discuss the types of connectors available for in-vehicle connectivity.
a) The Molex Mini50 Connector System provides reliable performance in a limited space, making them suitable for applications such as infotainment, lighting, and HVAC systems. Mini50 sealed and unsealed wire-to-board headers and receptacles allow device manufacturers to package circuits in tighter spaces by utilizing smaller pin, terminal, and wire sizes.
b) The stAK50h Unsealed System's stackable nature allows easy connection and eliminates the need for custom tooling. It offers unsealed hybrid headers and receptacles that deliver both signal and Ethernet connectivity within a small footprint. The stAK50h Unsealed Connection System's headers, and receptacles are color-coded to enable quick identification and easy assembly.
c) The Molex TAK50 Terminal is designed to provide high-current density and robustness, and the ConnTAK50 Connector System offers a new miniaturized solution for signal-based applications in and surrounding a vehicle. The 2-piece construction provides significant mechanical and electrical advantages over competitor terminals and provides durability and reliability.
d) The DuraClik Connector System features a wide latch that provides an audible click, ensuring a secure mate. The DuraClik Wire-to-Board Connector System features TPA (terminal position assurance) and ISL (independent secondary lock) options, with the ISL option providing a high retention force for improved reliability in rugged environments. It is available in 2 to 15 circuits in single-row configuration with vertical and right-angle orientations. The DuraClik family provides superior electrical contact reliability, mating retention, and design flexibility for high-vibration applications.
e) The H-DAC 64 connector system provides single- and dual-row options and is designed to offer space-saving alternatives. It satisfies all unsealed USCAR-2 class 2 requirements. A positive lock ensures proper mating, and a TPA feature increases terminal retention. The single-row connector system consists of vertical and right-angle, 4-circuit headers, while the dual-row connector system offers 6- to 20-circuit configurations and a 24-way hybrid connector.
f) To solve today's vehicles' growing electronic device requirements, Molex developed a modular 0.64, 1.50, and 2.80mm terminal header system. The Stac64 connection system allows OEM and device manufacturers greater design flexibility to support both low-level signal requirements and power applications up to 30.0A. The Stac64 system enables automotive manufacturers to use header assemblies as stand-alone components to gang multiple headers to support an extensive range of signal and power needs for devices and modules. The standard product line based on the 0.64mm pitch terminal includes 8-, 12-, 16- and 20-circuit connectors in both vertical and right-angle headers supporting low-level signal and power requirements.
g) The HSAutoLink Interconnect system takes advantage of Molex's experience at producing high-speed cable technology, which meets the needs of the emerging connected vehicle. HSAutoLink has the required bandwidth to support advanced infotainment, telematics, and camera devices spanning the commercial and automotive vehicle industries. The next-generation HSAutoLink Interconnect System offers a robust and sealed system with data rates up to 13.5 Gbps.
The HSAutoLink Interconnect System imports a USCAR-30 compliant solution for point-to-point in-vehicle connections, complete with multiple keying options and full-length cable shielding for improved signal performance reduced Electro-Magnetic Interference (EMI). The USCAR-30 compliance ensures products to be duly qualified and market-tested to withstand the demanding in-vehicle environment.
It supports multiple high-speed communication protocols like USB 2.0, USB 3.1 (5 Gbps), LVDS (8 Gbps - 4 GHz per lane), and DisplayPort, FDP-LInk4 (13.5 Gbps), as illustrated in the following table. The HSAutoLink II Interconnect System supports high-speed media protocols, including USB 3.1 (5 Gb/s data rate).
HSAutoLink I | 4 and 5 Circuit, USB 2.0, LVDS, Ethernet |
HSAutoLink II Sealed and Unsealed | 6 and 12 Circuit; USB 2.0, 3.0, LVDS, DisplayPort, Ethernet |
HSAutoLink Hybrid Unsealed | 14 Circuit; USB 2.0, 3.0, LVDS, DisplayPort, Ethernet |
Table 1: HSAutoLink Interconnect System
h) CMC and CMX Sealed Connectors
The CMC and CMX connector family is an IP6K9k sealed, high-density, hybrid modular connector system designed for high-conductivity applications in demanding environments. These connection systems are employed in powertrain applications, including ECUs, compartment applications, suspension systems, gearboxes, and electronic parking brakes.
Standard CMC headers for wire-to-board connections are available in various off-the-shelf 1-, 2- or 3-pocket configurations. Standard version CMC hybrid connectors hold two distinct terminal sizes, 0.635mm (.025") and 1.50mm (.059"). Power version CMC hybrid connectors hold three distinct terminal sizes, 0.635mm (.025"), 1.50mm (.059") and 2.80mm (.110"). Both connector versions function between -40 and +125°C operating temperatures.
CMC hybrid connectors and mating headers offer sealed, high-density, modular, and economical wire-to-board and wire-to-wire connection systems for heavy-duty powertrain body-electronics applications in automotive and commercial vehicles.
High-density CMX Sealed Connectors are intended to meet the low- and medium-current requirements of space-restricted electronic control units and other wire-to-board transportation applications.
Figure 10: CMC (a) and CMX (b) Sealed Connectors (
Copyright Molex)
i) High-Speed FAKRA Mini (HFM)
High-Speed FAKRA Mini (HFM) Coaxial Cable is capable of carrying 20 GHz of data speed. Supported applications include instrument clusters, ADAS, camera modules, GPS antennas, gateways and switches, 4K displays, infotainment, internet, navigation, nextGen wireless LAN, sensors, and surround-view. It offers design flexibility and is available in unsealed, sealed, and in-line connectors and in right angle and vertical PCB plugs and plug jacks. The 4-port HFM solution reduces PCB footprint by 48% on the front edge of a PCB.
- 5.3 Microminiature Connectors
Molex micro wire-to-board, memory card, board-to-board, wire-to-board and FFC/FPC connectors are designed to satisfy requirements like smaller size and higher performing technologies. This means better performance in a compact space. Products range from a low of 42AWG to 0.35mm pitch spacing, multiple circuit sizes, up to 20Gbps speeds, and multi amps per circuit. These connectors are suitable for designers who require space savings, durable connector designs, and high-density signals. We will further discuss microminiature FFC/FPC and SlimStack Connectors suitable for automotive applications.
Easy-On FFC/FPC Connectors
Easy-On FFC/FPC Connectors are super-fine pitch and small-size, with ZIF, non-ZIF, slider, and flip-actuator styles. These connectors are available in a variety of circuit sizes to deliver both high reliability and fast data rates. These connectors have a 0.20 to 2.00mm range terminal pitch.
SlimStack Board-to-Board Connectors
The SlimStack Connector Family is suitable for space-constrained automotive board-to-board applications. These connectors offer a wide selection of low-profile, narrow width options in various mated heights and circuit sizes. They are available in multiple pitch sizes, mated height measurements, and circuit sizes to deliver design flexibility while meeting tight-packaging needs.
- 5.4 Applications
In this section, we discuss a variety of applications where connectors designed for in-vehicle electronic systems are utilized.
a) ADAS Camera IO Module
ADAS/AD functions depend on data transmission originating from sensors and cameras. Cameras are crucial sensors for almost all ADAS applications; a single car may need as many as six cameras for ADAS applications. They must be located where they can trace external (outside of the vehicle) objects. These cameras will be subjected to dust and water sprays. Molex Camera Backshell Assemblies are designed with IPX7 and IPX9K sealing classes to prevent dust and water ingress, and deliver weather-resistance and provide rugged and easy-to-implement connectivity to the increasing number of cameras needed.
To support the increased demand for car camera modules with high-speed video processing, Molex provides camera I/O backshells with coaxial bullet and jack interconnections supporting high-speed media protocols with frequencies up to 3 GHz. Shown here is an ADAS Camera Backshell Assembly that uses a Camera Backshell Housing Assembly (68592 Series), Camera I/O Bullet, Camera I/O Jack (20879 Series), SlimStack B-to-B Connectors, 0.40mm Pitch Floating, FSB5 (203955 and 203956 Series). Molex provides camera I/O backshells with coaxial bullet and jack interconnections supporting high-speed media protocols.
b) ADAS/AD ECU
ADAS is intended to minimize, as much as possible, the driver's workload throughout the drive. In this concept, vision systems encircle the vehicle, effectively placing the vehicle inside a protective bubble to stop driver error. Using their visual processing capabilities, these systems feed tracking and recognition particulars to the onboard safety systems for driver drowsiness detection, collision avoidance, lane departure warning, and other protective features. Superior and reliable high-speed data are required due to the rapid increase of electronic control units (ECUs) and interior and exterior sensors to advance telematics and infotainment systems.
Molex supports customers in ADAS development to increase transportation and road safety. It uses SlimStack Board-to-Board Connectors, Floating FSB3 (Receptacle: 204927-0**1: Plug- 204928-0**1) and FSB5 Series (Receptacle: 203955-0**3: Plug- 203956-0**3) to connect the main PCB and different front PCBs. It provides wide floating ranges, flexible mating heights, and one of the smallest sizes in its category. The intelligent design allows robotic assembly and meets small space requirements, which are important to achieving miniaturization in the ADAS system.
c) LiDAR
LiDAR offers vehicles the critical spatial awareness they need to achieve autonomous operation. It uses laser light and time-of-flight (ToF) principles to generate a 3D map of the vehicle's surroundings. LiDAR offers the solution for mainstream vehicles, as multiple sensors are positioned around the vehicle and have their data combined to give a field-of-view. LiDAR can both detect an object and calculate its distance. LiDAR functions by sending out a light beam that will bounce off any objects within range, and a part of the signal will return to the LiDAR unit and be detected.
LiDAR uses Easy-On FFC/FPC Connectors, FD19 Series (505110 Series), 0.50mm pitch for connecting front main PCB and Rear PCB (P/N: 505110). The dual contact design and positive locking features ensure a reliable connection. An assortment of actuator options, including zero insertion force (ZIF), slider, and flip, help establish a secure connection between the FFC/FPC connectors and terminals.
d) RADAR
Radar is essential to ADAS systems, and is frequently used in conjunction with multiple other systems like LiDAR, ultrasonic, and vision sensors. Radar sensors are generally mounted on all four sides (front, rear, left, and right) of a vehicle. Components for radar applications must deal with automotive environment stresses, including vibration and shock. It operates effectively over long distances and in poor weather conditions. The initial operating frequency used was 24GHz, although 77GHz solutions now supersede this. Long-range radar (LRR) is capable of detection at distances up to 250 meters, while medium-range radar (MRR) operates in the 1-60 meters range, and short-range radar (SRR) covers the 1-30 meters range.
Molex supports customers in the development of Radars that increase transportation and road safety. It offers small pitch sizes from 0.20 to 2.00mm that are crucial for space-constrained ADAS applications. Radar uses SlimStack Board-to-Board Connectors, 0.40mm Pitch Floating, FSB3 (204927 and 204928 series), and Easy-On FFC/FPC Connectors 0.50mm Pitch, FD19 (505110 Series) to connect the main PCB to other front PCBs.

Figure 18: Power Control Unit (
Copyright Molex)
e) Power Control Units
Design needs for control units and their management have evolved with electric vehicles' rising popularity (and adoption). Most EVs substitute mechanical control systems with electronic versions, and such replacements need flexible and compatible micro products. Conservation of space is vital for contemporary automotive engineers, as they need components that provide high quality, reliability, and resistance to heat and vibration, while being designed for miniaturized space requirements.
Power control units deploy several parts, namely Easy-On FFC/FPC Connectors, 0.50mm Pitch, FD19 (505110 Series), SlimStack Board-to-Board Connectors, 0.635mm Pitch Floating Receptacle (209168 Series), SlimStack Board-to-Board Connectors, 0.635mm Pitch Plug (53627 Series) to connect the Top PCB with the main PCB. SlimStack Board-to-Board Connectors, Floating FSB3 and FSB5 Series, offer wide floating ranges, flexible mating heights, and one of the smallest sizes in its category.
f) Central Information Display
Safety, user experience, and connectivity continue to push future digital cockpit developments. There is demand for simpler, more user-friendly information management inside the vehicle-all while anticipating new capabilities, including automated driving and seamless mobile device integration.
Vehicle manufacturers insert instrument cluster applications as part of digital cockpit domain controllers. Molex's Board-to-Board, FFC/FPC, I/O camera, and backshell solutions offer various connectivity supporting next-generation information management in digital cockpit designs. The Central Information Display uses Easy-On FFC/FPC Connectors, 0.50mm Pitch, FD19 (505110 Series) to connect main PCB and touchscreen LCD monitor. FFC/FPC connectors are available with a range of pitches and circuit sizes combined with ZIF, non-ZIF, slider, flip actuators, and locking features that deliver both reliability and user-friendliness. They offer versatility, with terminal pitches that range from 0.20mm to 2.00mm for applications from tiny wireless earbuds to automotive. This connector has six actuators: Front Flip, Back Flip, Non-ZIF, Slider, Flexi-Latch, One-Touch. It works with generic FFC cables, eared/notched FFC cables for locking feature, or custom FPC cables.
6. Glossary
- ADAS: An advanced driver-assistance system is an electronic system used to assist the driver with advanced technologies.
- CAN: The Controller Area Network bus is a robust serial communication protocol used in automotive networks to address high bandwidth.
- ECU: An Engine control unit or electronic control unit is an electronic device that controls all the vehicle's engine functions.
- FFC: Flexible Flat Cables (FFC) are a kind of electrical ribbon cable consisting of a plastic film to which multiple metallic connectors are bonded.
- FlexRay: It is an automotive network communications protocol developed by the FlexRay Consortium. It offers flexible configurations, with support for topologies such as bus, star, and hybrid types.
- FPC: A Flexible Printed Circuit is an electronic circuit board consisting of a flexible polymer base that is lighter, thinner, and offers increased flexibility in connectivity.
- LiDAR: Light Detection and Ranging comprise an optical analog of radar, providing high spatial resolution range information.
- MIMO: Multiple Input Multiple Output is a wireless technology that uses multiple transmitters and receivers to simultaneously transfer data.
- PCB: A Printed Circuit Board supports and connects electronic components using conductive traces and pads.
*Trademark. Molex
is a trademark of Molex Corporation. Other logos, product and/or company names may be trademarks of their respective owners.

Test Your Knowledge
Connectors VI
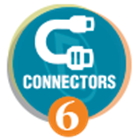
Are you ready to demonstrate your knowledge of Automotive Connectors used for In-Vehicle Electronic Systems? Then take a quick 15-question multiple choice quiz to see how much you've learned. To earn the Connectors VI Badge, read through the learning module, attain 100% on the Quiz, and leave us some feedback in the comments section.